ギヤノイズとは(その原因と歯車製造時の注意点)
歯車(ギヤ)はあらゆる製品に使用されています。一方で、騒音の原因にもなるため、発生要因を理解し効果的な対策を講じることは、製品の性能や耐久性を向上させる上でも必要不可欠です。
この記事では、ギヤノイズの定義や原因、そして歯車製造における注意点について解説します。
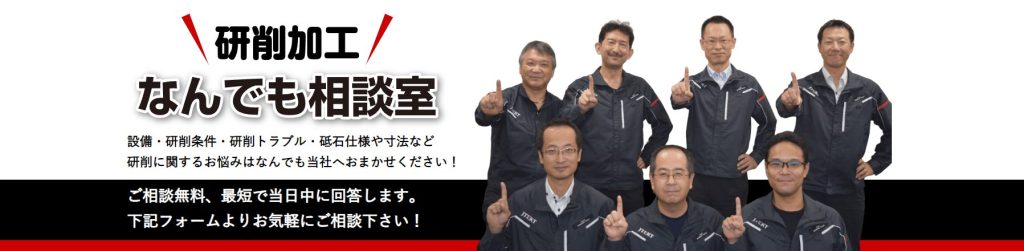
目次
ギヤノイズとは
歯車(ギヤ)の運動に伴う騒音、通称ギヤノイズは、大きく分けて「うなり音」と「歯打ち音」に分類されます。それぞれの特性とノイズが生じる条件を見ていきましょう。
うなり音は、一般的に高周波数の振動音であり、歯数の連続的な接触により発生します。うなり音は高い音色で音圧レベルとしてはさほど大きくありませんが、不快な音として敬遠されがちです。これは、歯面形状の誤差や歯車の剛性に問題がある場合に発生します。
一方、歯打ち音は低周波数の振動音で、歯車の一部が他の部分と衝突することによって発生します。負荷の変動や、バックラッシと呼ばれる意図的に設けられた歯車の「隙間」や「遊び」が不適切(過大または過小)であるときに発生する現象です。
歯車が回転するとき、その表面の微小な凹凸や形状誤差が原因で、歯車同士が完全には噛み合わない場合があります。歯車同士の接触点が一定でないと、接触点の移動や歯車の変形が生じ、これが振動となってギヤノイズとして現れます。
このように、ギヤノイズは歯車の製造過程や運動中の微細な異常から生じるものであり、その対策には高い技術が求められます。
ギヤノイズの原因
ギヤノイズは、製造の誤差やバックラッシ、負荷の変動など、さまざまな要素が原因となり発生します。この章では、それぞれがどのようにギヤノイズを引き起こすのかを解説します。
製造誤差
製造誤差とは、製造過程で生じる予期しない差異のことを指します。これらの差異は、歯形や歯すじの形状、ピッチなどの微細な誤差として現れ、結果として歯車のパフォーマンスに影響を及ぼしてしまいます。
ギヤノイズの原因のひとつとして挙げられるのが「表面粗さ」や「うねり」です。これらは、歯車の表面に微小な凹凸が存在する状態を指します。
「表面粗さ」や「うねり」があると、振動が増大しノイズが発生します。特にμm単位の歯面の微小な凹凸(うねり)は、裸眼では確認できないほど微細な差異ですが、これが積み重なるとノイズとなって現れます。
さらに、「傷」もギヤノイズの原因のひとつです。歯車の表面に傷があると、それが他の歯車と接触するたびにノイズが発生します。
バックラッシ
バックラッシとは、歯車が噛み合っている状態で、一方の歯車を固定したまま他方の歯車を回転させたときに生じる、歯車の「隙間」や「遊び」のことです。適切なバックラッシは歯車をスムーズに動作させ、摩擦や熱を抑える役割を果たします。
しかし、バックラッシが大きすぎる場合、歯車同士の歯の噛み合いが悪くなりギヤノイズの発生に繋がります。
逆にバックラッシが小さすぎると、歯車同士の接触面積が増え、摩擦や熱が増大します。これは歯車の耐久性を低下させるだけでなく、ギヤノイズの原因にもなります。
負荷変動
負荷変動は、ギヤノイズの原因のひとつです。歯車に重荷重がかかったり変速したりする場合、歯面にかかる負荷は均等に分散せず、一部の歯に集中することがあります。この結果、歯車の歯が一時的に曲がったり、振動したりするのです。
特に、重荷重の下では、歯車の歯が過度に変形する可能性があり、ギヤノイズの主な発生源となり得ます。
変速時にも、一部の歯が他の歯よりも多くの負荷を受ける可能性があります。これが結果的に歯車全体のストレスを増加させ、ギヤノイズを引き起こす可能性があるのです。
したがって、歯車を製造する際は、これらの負荷変動を考慮に入れることが必要不可欠です。これにより、歯車の寿命を延ばし、機械全体のパフォーマンスを向上させ、ギヤノイズを最小限に抑えることもできます。
歯車研削の重要性と注意点
ギヤノイズを最小限に抑えるためには、歯車の精度が非常に重要です。特に、歯車を作る過程で行われる研削加工はその品質を大きく左右します。研削時には、歯形や歯すじの形状誤差、ピッチ誤差、1μm単位の歯面の微小な凹凸(うねり)、表面粗さなど、多くの要素に注意を払う必要があります。これらを適切に管理しなければ、ギヤノイズは抑制できません。
この章では、これらの研削作業で注意すべきポイントを解説し、最適な歯車製造のためのヒントを紹介します。
歯形や歯すじの形状誤差
歯形や歯すじの形状は、歯車の性能に大きな影響を与えます。これらの形状は、歯車がスムーズに噛み合い、正常に動作するために必要な条件です。
研削は加工者の技量や気温などの「環境」に左右されやすい工程とされていますが、高精度のCNC研削盤であれば、安定して正確な形状を作り出すことができます。
また、適切な研削砥石やドレッサの選択も必要不可欠です。これらのツールは歯車の表面を滑らかにし、精度を保つために使用されます。砥石はその性能を維持するために、定期的なメンテナンスや交換が欠かせません。定期的にドレッシング(目直し)を行い、砥石の研削面をしっかりと整えましょう。砥石、ドレッサなど研削工具には寿命があるため、定期的に交換することも必要です。
歯車の製造過程では、正確な歯形と歯すじの形成、適切な研削ツールの選択と維持管理が重要なポイントです。これらを怠ると、ギヤノイズの原因となる製造誤差が生じ、歯車の性能が低下する可能性があります。
ピッチ誤差
ピッチ誤差とは、製品の実際のピッチと理論上のピッチとの差のことです。これが生じると、歯車同士の噛み合いが悪くなり、伝達効率が低下したり、ノイズが大きくなったりするなどの問題が生じます。製造工程では、研削工程での精密な位置決めシステムが重要な役割を果たすのです。
ピッチ精度を確保するためには、歯車の歯と歯の間隔を正確に保つことが必要です。そのため、研削工程で使用する機械の設定や調整が求められます。それぞれの歯車の形状やサイズに合わせて、歯車を正確な位置へと誘導するシステムが必要不可欠です。
また、時間と共に機械の精度は狂っていきます。機械の精度を保つためには定期的な較正が欠かせません。一定の間隔で研削機の較正を行うことで、常に最適な状態で歯車を加工することができます。
歯面うねり(μm単位の微小な凹凸)
μm単位の歯面の微小な凹凸(うねり)は、製造工程において、歯車の性能を左右する重要な要素のひとつです。1μmという大きさは、髪の毛の直径に比べて約100倍も細かいスケールです。それほど精密な加工をしなければ、歯車同士が絡み合う際に生じる摩擦や衝撃、そしてそれによるギヤノイズを最小限に抑えることができません。
微小な凹凸、いわゆる「うねり」が発生すると、摩擦が大きくなり、結果としてギヤノイズを引き起こします。特に大きな負荷がかかる状況下では、この「うねり」が歯車の寿命を短縮させる原因にもなり得ます。製造段階では「うねり」を極力抑え、1μm単位の寸法精度を確保することが求められるのです。
歯車研削のプロセスにおいては、研削速度、送り速度、研削負荷などのパラメータを最適化し、歯面のうねりを最小限に抑えることが求められます。
また、研削砥石の品質も歯面仕上げに大きく影響します。砥石の選定時には、材質や形状、硬度などを考慮に入れ、最適なものを選択しましょう。
表面粗さ
歯車の表面粗さは、摩擦や摩耗、そして効率に直接影響を及ぼします。それゆえ、表面粗さの改善は歯車の品質向上にとって欠かせません。
表面粗さを改善するためには、まず研削砥石の選択が必要です。具体的には、粒度と硬度が適切なものを選ぶことが求められます。これらは研削精度や効率を左右し、結果的に歯車の表面粗さに影響します。
さらに、研削液の選択も重要です。適切な研削液を使用しなければ、研削中の冷却効果と潤滑性を確保できません。適切な研削液を選定すれば、熱損傷を防ぎ、表面品質を向上させることができます。
これらの細やかな点に配慮することで、歯車の表面粗さを改善し、ギヤノイズの発生を抑制できます。
ジェイテクトグラインディングツールの歯車研削用ドレッサ「UPドレッサプレミアム」
「UPドレッサプレミアム」は、高精度かつダイヤラップ量の最適調整と均等化、高硬度めっきでのダイヤ保持力向上により安定した品質が得られます。
上記特長により、高精度なドレス形状による歯面精度の向上、長寿命による工具費の削減、最適化されたダイヤ作用面積によるドレス抵抗の低減を可能にし、歯車研削における生産性向上に貢献致します。
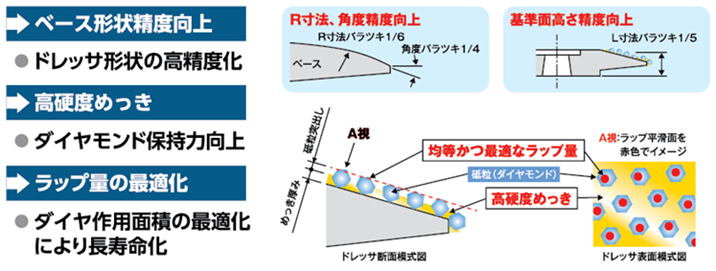
ギヤノイズに影響する要因の1つ、歯面うねりに関する評価事例をご紹介致します。
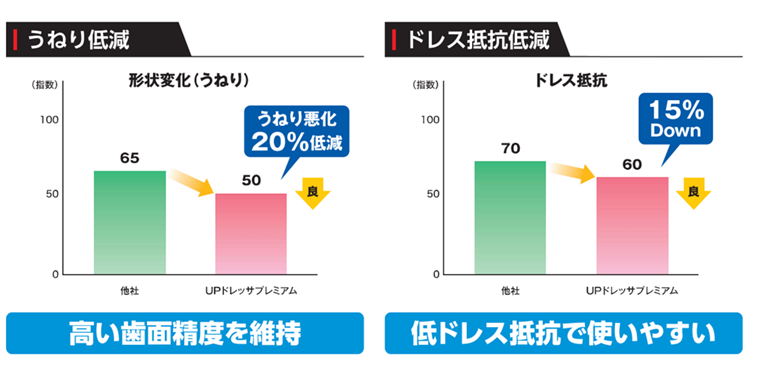
本ドレッサでは、他社品と比較してドレッサうねり変化を23%低減、ドレス抵抗を15%低減を実現しております。
また弊社従来品と比較してドレッサ寿命が125%向上しております。
製品についてのお問合せや、その他研削加工に関する些細なご相談はこちらからお問い合わせください。