セラミックス(SiCとアルミナ)の特性と加工方法
アルミナやジルコニア、SiCなどのファインセラミックスは、セラミックスの中でも高精密で高性能なセラミックスとされ、半導体や自動車、医療関連など、幅広い産業分野で利用されています。
本記事では、ファインセラミックスの中でも上記分野などで多く利用される、「SiC(炭化ケイ素)」と「アルミナ」の特性と加工方法について事例を交えて解説します。
目次
SiCとアルミナ
ここでは、SiCとアルミナの特性や主な用途について解説します。
SiCとは
SiCは、ケイ素(Si)と炭素(C)から構成されるセラミックスです。
化学的に非常に安定しており、融点が約2,700℃と高く、酸やアルカリにも強い耐食性を示します。物理的には、新モース硬度において13(ダイヤモンド:15)と非常に硬い材料であり、熱伝導率はアルミニウムと同程度です。また、熱膨張率が小さいため熱衝撃にも強く、急な加熱や急冷でも部材が歪んだり破損しにくいところも特徴です。
SiCは高温環境にさらされる、ディーゼルエンジン車のマフラー、半導体製造におけるエッチングやCVD装置の部材に使用されてます。
アルミナとは
アルミナは化学式Al2O3で表される酸化アルミニウムの通称です。
SiCと同様、化学的に非常に安定しており、融点が約2,000℃と高く、強い耐食性を示します。物理的には、SiCに次ぐ硬度(新モース硬度:12)を持っています。また、高い電気絶縁性を持つことも特徴です。
比較的安価に入手できることから、セラミックスの中でも最も広く利用されている材料です。
半導体分野では、製造工程において不純物混入(コンタミネーション)を嫌います。そのため、半導体を製造する装置においても、長期稼働による摺動部の摩耗による摩耗粉の発生を抑制する事が不可欠であり、金属や有機物ではなく、耐摩耗性に優れたアルミナセラミックスが用いられます。
以上のように、アルミナは優れた物理的・化学的特性を有するセラミックス材料であり、さまざまな分野で幅広く利用されている材料です。
セラミックス(SiCとアルミナ)の加工特性
前述のように、SiCやアルミナは、優れた特性を有し、幅広い産業分野で使われる材料です。その一方で、セラミックスは一般的に硬脆性などの特徴から、加工時には注意すべき点がいくつかあります。ここでは、SiCやアルミナを例に、セラミックスの加工特性を解説します。
硬脆性材料であるSiCとアルミナ
SiCやアルミナなどのセラミックスは、高硬度である反面、脆い材料でもあります。
このような材料を「硬脆材料」と言います。このような硬脆材料の切削や研削では、硬くて工具の刃が切込みにくく、いざ切り込むと脆いために欠け(チッピング)が発生してしまう、非常に加工が難しい材料です。
SiC・アルミナの研削加工
研削加工は、砥石を高速回転させて、工作物の表面を削っていく加工方法で、表面を滑らかに仕上げたい場合や、高い寸法精度の加工が必要な場合に用いられます。
SiCやアルミナの加工では、硬脆性材料の特徴から切削による加工が困難なため、仕上げ加工としてダイヤモンドを使用した超砥粒ホイールで研削加工を行います。
セラミックス研削加工の課題となるチッピング
前述のとおり、セラミックス加工ではチッピングの発生が問題となります。
チッピングが発生すると、見た目の悪さ、製品の寸法精度の低下、欠けた部分から割れが進行して破損し、部材の強度品質低下につながるなどの問題が生じます。そのため、チッピングを抑制するために最適な工具の仕様選定や研削条件で加工を行うことが重要です。
セラミックス研削加工のチッピング対策
チッピングの発生を抑え、高品質な研削加工を実現するためのより詳細な対策については、下記をご覧ください。
この章では、セラミックス研削においてチッピング量が砥粒径以下になった後、更にチッピングを低減したい場合の有効的な対策方法をご紹介いたします。
チッピング量とは欠けの深さのことであり、欠けの深さは砥粒切込み深さに依存します。
砥粒切込み深さを小さくできる3つの対策案と、各対策がチッピング量にどう影響するのかをご説明いたします。
砥粒切込み深さを小さくし、チッピング量を低減するには、
- クリープフィード研削に変更する
- 研削能率を下げる
- 砥粒細粒化
などの対策が有効的です。
クリープフィード研削とは、工作物の送り速度を遅くする代わりに、切込み量を100倍~1000倍にあげて研削する方法です。工作物の送り速度を下げることで、砥粒切込み深さも小さくなるため、研削能率を下げすぎることなく、効果的にチッピングを抑制することができます。一方で、ホイールと工作物の接触長さが長くなるため、熱負荷は大きくなります。研削液の供給圧を上げる、切れ味の良い仕様のホイールに変更する、などの対策を検討しましょう。
研削能率を下げることも、チッピング抑制に有効的な対策ですが、一方で生産性は下がります。チッピング量とのバランスを見て、砥粒細粒化も検討してみましょう。
集中度を変更せずに砥粒径を細粒にすると、単位体積当たりの砥粒数が増えるため、砥粒間距離は小さくなります。砥粒間距離が小さくなることで砥粒切込み深さも小さくなり、チッピング量を低減することができます。
SiC研削加工のチッピング抑制事例
弊社事例ではSiC研削において、研削方式をハイレシプロからクリープフィードに変更したことでチッピング量を71%低減、研削能率を下げることにより3%低減、砥粒径の細粒化(#170⇒#400)により14%低減しました。
取り代は加工目標時間と前加工の欠けより調整しましょう。
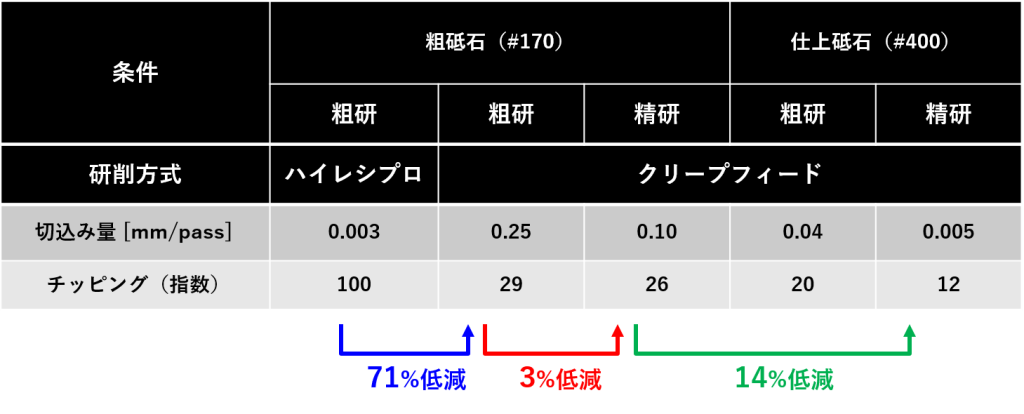
上記事例のように、これらの対策を組み合わせることで、SiCやアルミナの加工におけるチッピング量を効果的に抑制することができます。
半導体産業で使用されるSiCとアルミナの研削加工事例
この章では弊社でのSiCやアルミナの具体的な研削事例をご紹介します。
SiC製治具の研削加工
ジェイテクトグラインディングツールでは、レジンホイール「レボメイト」を用いてSiC治具の平面研削を行ったところ、ドレスインターバルが従来レジンホイールに比べ1.4倍に向上。切込み量を3倍にすることができたため、加工時間はこれまで3日かかっていたものが1日に短縮されています。ドレス頻度低減かつ加工時間短縮を実現し、生産性向上に貢献します。
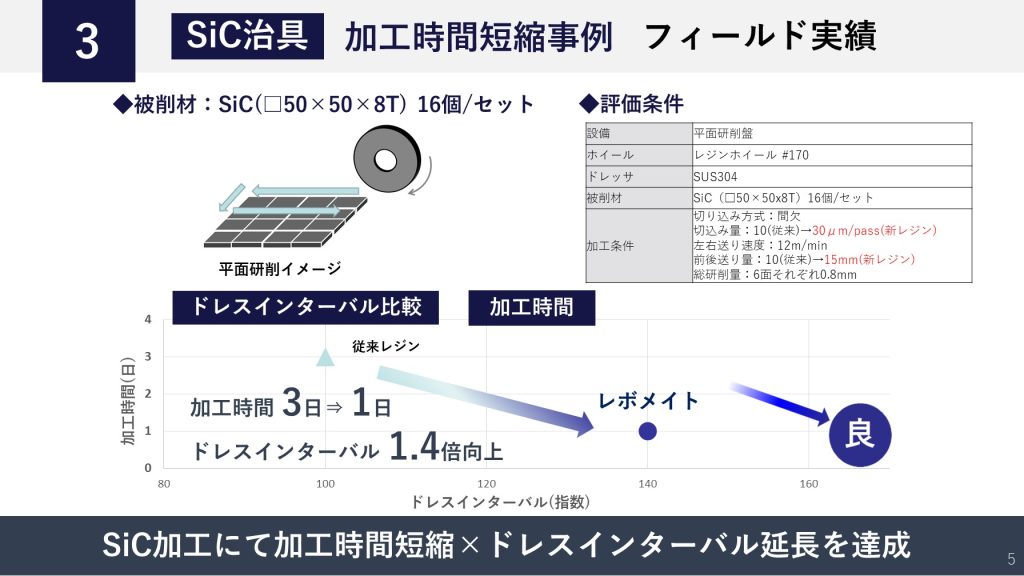
アルミナ製治具の研削加工
半導体産業において、アルミナは半導体装置の治具やアルミナ静電チャックなどに使用されています。ジェイテクトグラインディングツールでは、レジンホイール「レボメイト」を使った平面研削で従来レジンホイールに比べ、ドレスインターバルが1.6倍に向上しました。さらに、ホイールの寿命は1.1倍に向上。砥石軸軸電流値は20%低減されています。ドレス頻度低減による段取り工数の削減、ホイール寿命向上によるツールコスト削減、研削抵抗低減によるサイクルタイムの短縮を実現いたします。
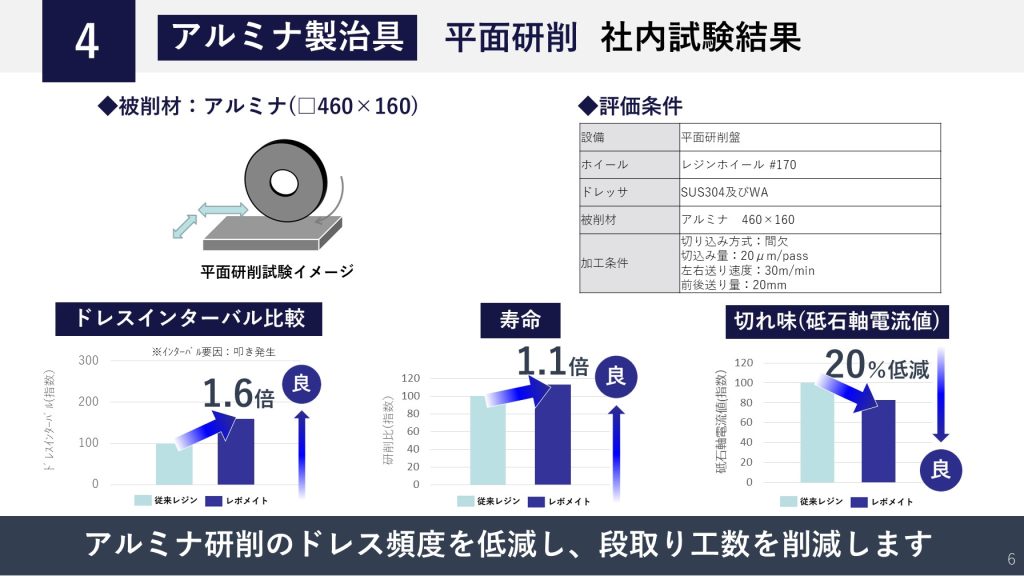
SiCとアルミナの研削加工におけるお悩みのご相談はジェイテクトグラインディングツールへ
SiCやアルミナなどの硬脆材料の研削加工では、チッピングの発生や加工に長い時間がかかると言った課題があります。このような課題にお悩みの際は、是非ジェイテクトグラインディングツールへお問い合わせください。