歯車製造における歯車研削の工程と方法
トランスミッションやe-Axleなどの変速機・減速機に使用される歯車製造では、騒音や振動の低減・伝達効率向上を実現するために、仕上げの歯車研削工程が重要です。この記事では、歯車製造における研削工程の重要性とその方法について詳しく解説します。
目次
歯車研削とは
歯車研削工程では、砥石を用いて歯車の歯面を精密に削り、規程の形状や精度に仕上げます。歯車研削を行うことで、歯車歯面の凹凸やピッチ誤差の低減、歯面粗さの向上などを可能にし、騒音や振動の低減、動力伝達率向上、歯車の疲労寿命の向上が期待できます。
歯車製造と歯車研削工程
歯車の製造工程は、最適な材料の選定から始まり、材料や製造方法に応じて、ブランク加工、歯切り、シェービング、熱処理、研削などのプロセスを経て製造されます。本章では、それぞれの工程の目的と注意点、工程における方法の種類を解説します。
材料選定
一般的に歯車の材料には、鋼材、鋳鉄、ステンレス鋼、非鉄金属(銅合金など)、樹脂などがあり、使用される環境・条件に応じて選定されます。例えば、高負荷条件下での使用を想定する場合、耐摩耗性や耐久性は重要な要素ですが、その分コストも上がるため、耐摩耗性、耐久性と製造コストを加味して適正な材料選定を行うことが重要です。
本記事では鋼材と鋳鉄の製造方法をピックアップして解説します。
鋼材
鋼材は、高い強度と耐摩耗性により、一般的に使用される歯車材料のひとつです。特に、高負荷や高速運転が求められる自動車や減速機などの工業用途で使用されます。鋼材には鉄をベースとした合金である炭素鋼と、炭素鋼にクロムやモリブデンなどの元素をある一定量含む合金鋼の2種類があります。合金鋼は添加する元素によって強度や硬度の向上が可能ですが、添加する金属元素が増えるとその分製造コストが上がります。特に高い強度や靭性が必要な自動車やトラックなどに使用される歯車には合金鋼が選定されます。
鋳鉄
鋳鉄製の歯車は、振動吸収能力を持ち合わせており、騒音が問題となる場合に有効です。鋼材と比較して強度は低いですが、加工性が良く安価であり、製造コストを抑えたい場合や、除去加工などの歯車成形法が実用的でない大型歯車の製造などに使用されます。
材料選定は製品の設計段階で行われ、使用される材料に応じて後続の製造工程(ブランク加工、歯切り、シェービング、熱処理、研削など)が決定されます。
ブランク加工工程
ブランク加工工程では、材料の外径や内径を旋盤によって成形していきます。 このとき直径や中心穴の寸法精度は歯車の滑らかな回転に影響するため、本工程は歯車製造における重要な工程の1つです。大型歯車では円筒状材料の切削による製造方法は除去加工が必要となり実用的ではないため、鋳造法などで製造されます。
歯切り工程
歯切り工程は、ブランク工程で基本形状に成形された材料を、工作機械を使用して歯車の歯を削り出し、歯車の原型を成形する工程です。歯切り方法にはホブ、ギヤシェーパ、ブローチ、スカイビングなどがあり、その方法と特徴を以下より簡単に説明します。
ホブ加工
ホブ加工は、円筒の外周にねじ状の切り歯を持ったホブカッターと呼ばれる工具を使用し、工作物とホブカッターを同時に回転させ、さまざまな方向から動かすことで必要な形の歯を削り出します。外歯車の歯切り工程で採用される加工方法で、動力伝達用歯車製造時に採用されることが多いです。
ギヤシェーパ加工
ギヤシェーパ加工は、刃物の往復運動により工作物を切削して歯切りを行う加工方法です。多段ギヤなど歯車近傍に干渉物があり、ホブの可動域が確保できない場合に採用される方法です。
ブローチ加工
ブローチ加工は、ブローチという工具を使用し、油圧を利用して下側に引っ張ることで内面加工し、歯溝成形する歯切り方法です。内歯車の歯切り工程で採用される加工方法で、引き抜きの一工程で完結するため加工時間が短く大量生産に向いています。
スカイビング加工
スカイビング加工は、工具と工作物を回転させながら、歯車をかみ合わせるように成形する歯切り方法です。ホブ加工よりも工作物形状に対する制約がなく、ギヤシェーパよりも高能率です。また、従来では内歯車と外歯車で加工方法を使い分ける必要がありましたが、スカイビングではどちらも対応でき、旋盤や穴あけも行う複合加工機で加工可能な点から工程が集約できることも特徴です。他の歯切り方法と比較しても、高能率・高精度が可能で近年注目されている歯切り方法です。
シェービング仕上工程
シェービング仕上げは、歯切り後に歯面を滑らかに仕上げる工程です。
歯面に複数の細かい切れ刃溝(セレーション)が入った歯車状のカッターを使用し、カッターを工作物に押し当てて切削することで歯面の粗さを整えます。歯面精度向上による騒音・振動の低減を目的として行われます。
熱処理工程
歯車の熱処理工程では表面処理を同時に行うことで、歯車のかみ合い部分の強度を高めることができ、摩耗に強い歯車を実現します。
以下より、焼入れ・焼き戻しの一般的な熱処理方法と、歯車製造時に採用される主な表面処理方法について説明します。
焼入れとは
焼入れとは材料の硬さを向上させるための熱処理方法です。ただし靭性(粘り強さ)は低下し、もろくなるので注意しましょう。具体的な方法としては、変態点以上まで加熱後、急冷します。焼入れ後は、必ず焼戻しを行います。
焼戻しとは
焼戻しとは焼入れ処理をして硬化した鋼材の粘りや靭性を高める作業です。
具体的な方法としては、変態点以下で長時間加熱後、急冷を行います。
焼戻しには低温焼戻しと高温焼戻しがあり、温度が高いほど硬度は減少しますが、靭性は増加します。
歯車製造時に表面処理とともに行われる代表的な焼入れ方法は、下記3種類あります。
浸炭焼入れ
炭素の含有量が少ない鋼材に適用され、表面に炭素を浸透させて焼入れを行うことで、表面を特別に硬化させる熱処理方法です。
窒化処理
材料表面に窒素を浸透させることで、表面を特別に硬化させる方法です。
具体的な方法としては、窒素を含む雰囲気中で長時間加熱をします。焼入れと焼き戻しは窒化の前に行います。浸炭焼入れよりも低温なため、材料の変形が少なく自動車部品など幅広い用途で使用されます。
高周波焼入れ
高周波誘導電流を利用して表面を加熱し、焼入れを行うことで、表面を特別に硬化させる熱処理方法です。
研削工程
研削は、歯車の製造工程における最終仕上げ工程で、高精度な歯車製造時に行います。歯車研削盤により高速回転する砥石を使って、歯車の歯面部分を研削します。特に熱処理によるひずみの大きい歯車製造時や、熱処理によるひずみのバラツキを低減するためには、歯車研削工程が必須です。高い精度で加工された歯車ほど、伝達能力の向上や騒音や振動の低減を実現します。
歯車研削の種類
歯車製造において研削は、製品の最終的な品質と性能に影響を及ぼす重要な工程です。 歯車研削における主な2つの研削方法の特徴とその使い分けを解説します。
成形研削
成形研削は、歯車の歯形と同じ形状に成形された切削工具を使用して、一歯ずつ精密に研削する方法です。この研削方法は、高精度な歯車製造に適しており、特に単品や試作品の製造に向いています。しかし、多数の歯形に対応した工具が必要であることや、位置決めが必要になり加工時間が長くなるなどのデメリットがあるため生産性には劣ります。
創成研削
創成研削は、ねじ砥石を使用して複数の歯を同時に研削する方法です。成形研削と比較して加工時間が短く、効率的に研削できるため量産に向いています。
歯車研削の重要性
歯車研削を行うことで、歯形や歯すじの形状誤差の低減、ピッチ誤差の低減、歯面粗さの向上などを可能にし、騒音・振動の低減、動力伝達の向上、高寿命な歯車製造を実現します。
歯形・歯すじ形状誤差
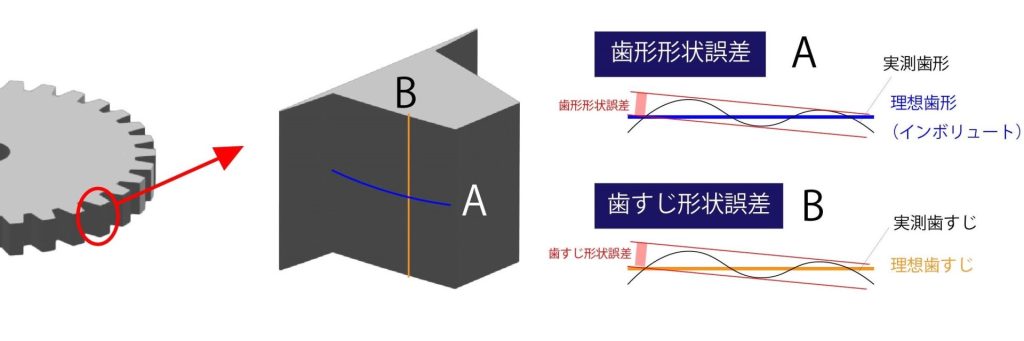
歯形・歯すじの形状は、歯車がスムーズに噛み合い、正常に動作するための重要な要素です。ねらいの歯形・歯すじ形状に対するミクロン単位の微小な凸凹(歯面うねり)は、かみ合い時の摩擦や衝撃などにより動力伝達効率が低下したり、騒音(ギヤノイズ)の原因となります。
歯形・歯すじ形状誤差の低減には、適切な研削砥石と高精度なドレッサの選定、またドレッサによる定期的な砥石の成形が重要です。
ピッチ誤差
ピッチ誤差とは、歯車の実際のピッチと理論上のピッチとの差のことです。これが生じると、歯車同士の噛み合いが悪くなり、伝達効率低下や騒音・振動などの問題が生じます。
ピッチ精度を確保するためには、歯車研削盤の剛性や歯合わせ精度が重要です。機械の精度を保つために定期的な校正も行いましょう。
歯面粗さ
歯車歯面粗さは、歯面の摩耗や伝達効率に影響を及ぼします。
歯面粗さを改善するためには適切な研削砥石を選定しましょう。砥粒の種類や粒度、結合剤が歯面粗さに大きく影響します。また、研削液の選択も重要です。適切な研削液を選定することで、熱損傷を防ぎ、表面品質を向上させることができます。
歯車研削における機械と工具
ここまで紹介したように、高精度な歯車の製造においては研削工程が重要になります。では歯車研削ではどのような機械や工具が使われているのでしょうか。
この章では、歯車研削に使われる機械と工具について解説します。
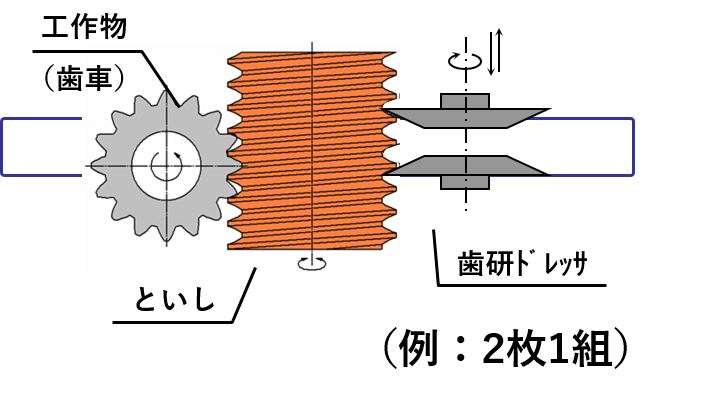
歯車研削盤
高速回転する砥石で歯車の歯面を仕上げる機械です。
歯車研削盤には「成形研削盤」と「創成研削盤」があり、用途によって使い分けられています。
歯車研削用砥石
歯車研削用砥石には、硬度の高い砥粒が含まれており、工作物に押し当てて高速回転することで、歯車の歯面を高精度に仕上げます。歯車研削用砥石にも様々な種類があり、歯車研削における高能率加工やドレスインターバルの向上など、製造環境に適した歯車研削用砥石を選択します。
歯車研削用砥石に採用される砥粒を紹介します。
普通砥粒系
普通砥粒系はセラミックス砥粒よりも硬度が柔らかいため、ドレス性がいいところが特徴で、ドレッサの寿命を延ばしてドレッサのツールコストを削減したい場合に最適です。
セラミックス系
セラミックス系は普通砥粒よりも硬度が硬いため、ドレスインターバルが長く生産性を向上したいときに採用されます。ただしドレス抵抗が高く、ドレッサ寿命が短くなります。
歯車研削用砥石に採用される結合剤を紹介します。
ビトリファイドボンド
ビトリファイボンドはガラスを主成分とした結合剤です。有気孔構造で切り屑が排出しやすく、砥粒保持力が高いため、切れ味が良くドレス性が良いところが特徴です。歯車研削用砥石では主にビトリファイドボンドが採用されます。
レジンボンド
レジンボンドは熱硬化性樹脂を主成分とした結合剤です。弾性率が高いため加工時の表面仕上げが滑らかになり、優れた仕上がりを実現します。さらに、ボンド後退性が良く新しい砥粒が表面に出やすいため、研削中も鋭利な状態を維持しやすいのが特長です。超仕上用の歯車研削ではレジンボンドが採用されます。
歯車研削用ドレッサ
歯車研削用ドレッサは、歯車用の研削砥石に使用するドレッシングツールです。砥石は使用するうちに摩耗し、形状や精度が低下するため、歯車研削用ドレッサによる定期的なメンテナンスが重要です。摩耗した研削砥石の表面を再形成し、必要な形状や精度を回復させることで、高精度な歯車の研削が可能となり、高品質な歯車製造を実現します。
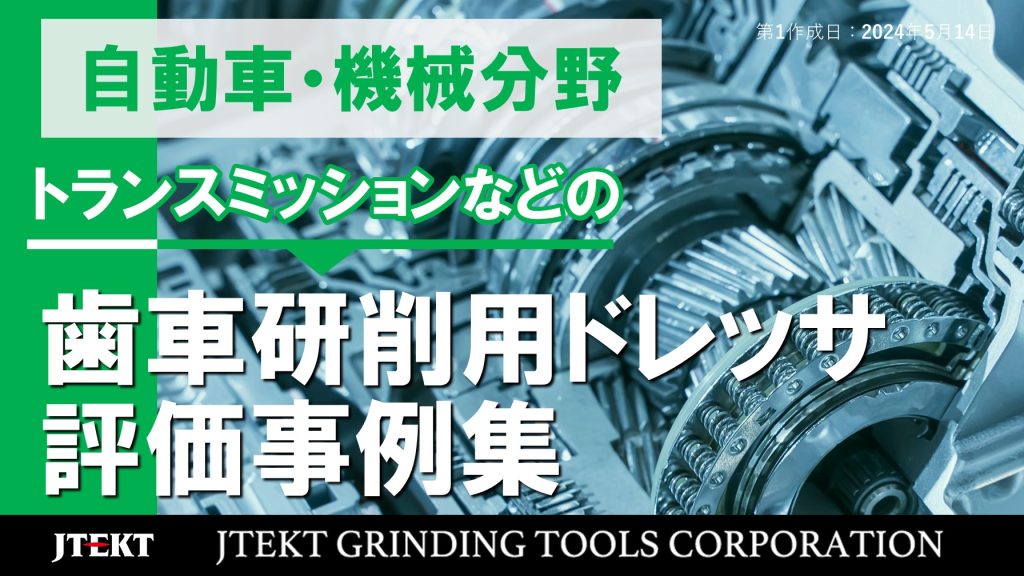
歯車研削用ドレッサの仕様
歯車研削用ドレッサは一般的にダイヤモンド砥粒を電着によって固定されたドレッサです。
歯車研削用砥石のドレスの重要性
歯車研削用ドレッサによるドレス作業では、目詰まりの除去と歯形形状、歯丈の修正を行います。ドレス作業の加工時間とドレッサ寿命のバランスを加味して、現状の課題に合ったドレッサを選択しましょう。
創成研削用歯研ドレッサ「UPドレッサプレミアム」のご紹介
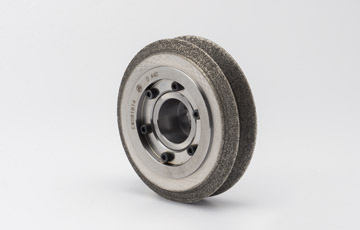
高精度かつダイヤラップ量の最適調整と均等化、メッキでのダイヤ保持力向上により安定した品質が得られます。
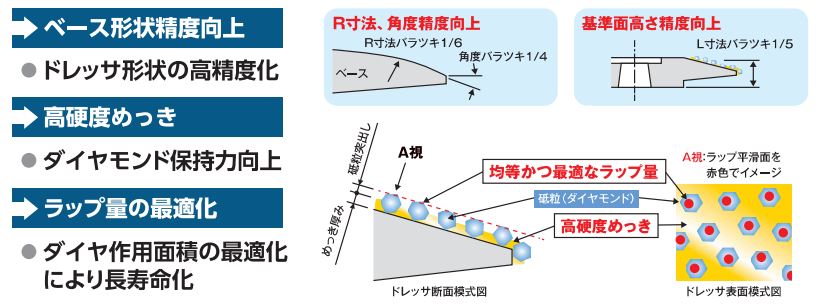
加工事例①ドレス抵抗とうねりを低減して高精度を実現
本ドレッサでは、他社品と比較してドレッサうねり変化を23%低減、ドレス抵抗を15%低減を実現しております。
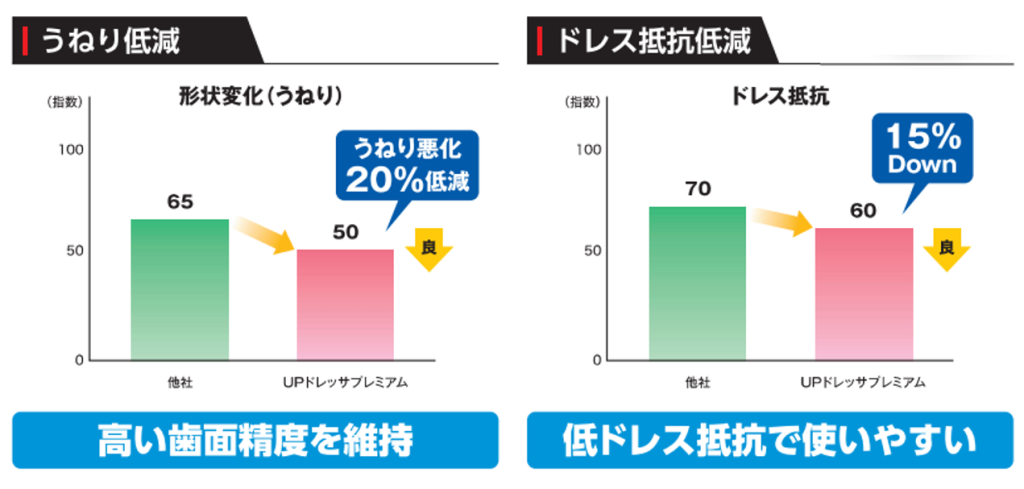
加工事例②高硬度めっき効果による歯先寿命向上を実現
弊社従来品と比較してドレッサ寿命125%向上を可能にし、ドレッサのツールコスト削減に貢献します。
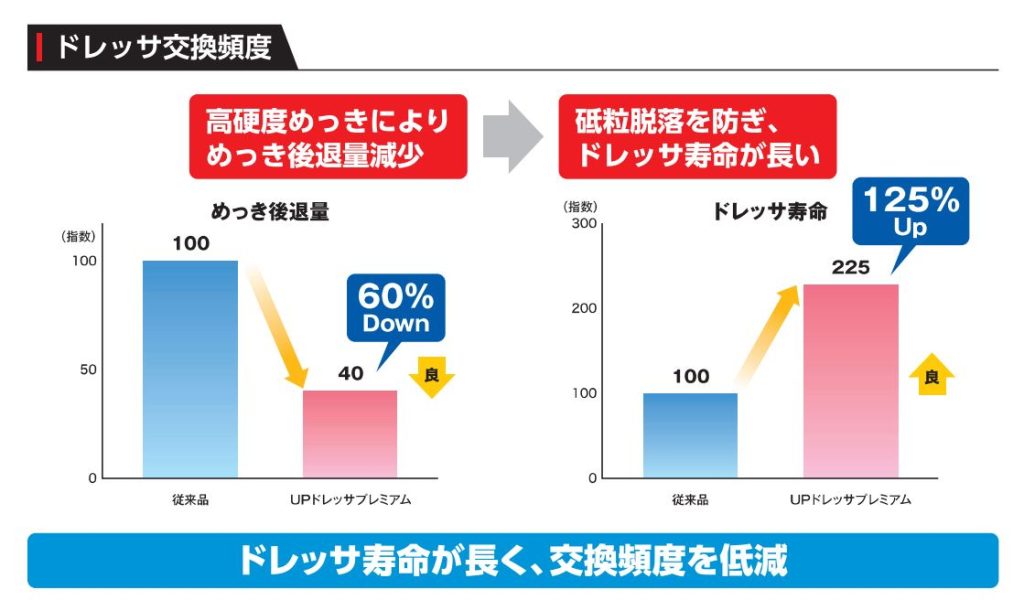
製品についてのお問合せや、その他研削加工に関する些細なご相談はこちらからお問い合わせください。