半導体製造における研削・研磨工程
半導体製造における研削・研磨工程は、微細な精度が要求される極めて重要な工程の一つです。この工程では、ウェーハ表面の平坦性や表面あらさを制御し、次の工程でのパターン転写や層の堆積を容易にするための準備が行われます。高度な技術と厳密な品質管理が必要なこの工程について、詳しく解説します。
目次
半導体製造工程の全体
はじめに、半導体の製造工程の全体を解説します。工程は大きく分けて次の4つになります。
マスク製造
半導体チップ上に配置する回路パターンを設計し、それを透明なガラス板の表面に描く工程です。回路パターンが描かれた透明な板をマスクと呼び、半導体ウェーハ上に特定のパターンを転写するために使用されます。これにより、半導体デバイスの微細な構造が定義されます。
ウェーハ製造
半導体デバイス基板材料となるウェーハを製造する工程です。ウェーハ製造では、スライシング、ベベリング、表面研削・研磨などの工程が含まれます。
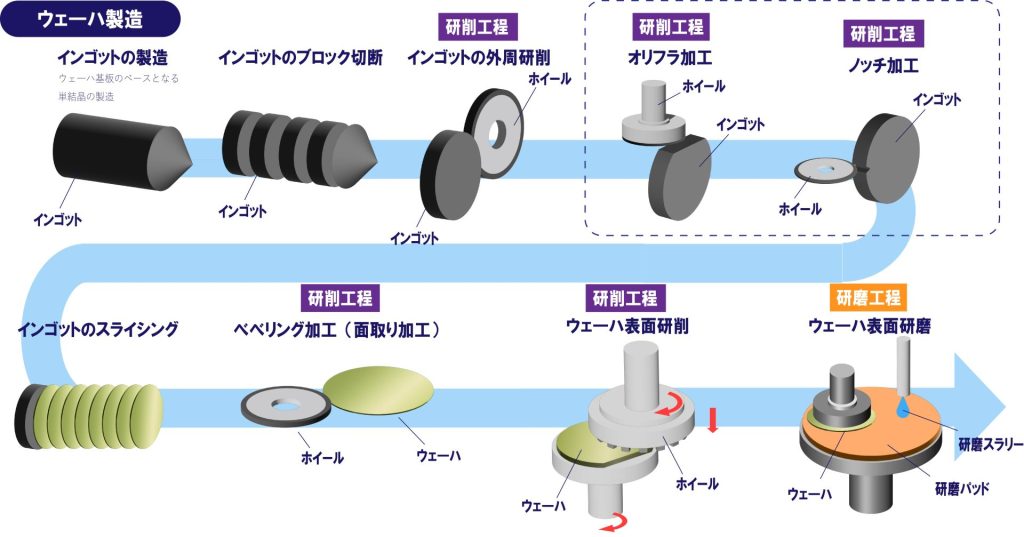
前工程
前工程は、ウェーハ上に回路を形成し、チップを作製する工程です。この工程には、フォトリソグラフィ、エッチング、イオン注入、洗浄、平坦化などが含まれます。フォトリソグラフィでは、マスクを使用してウェーハ表面にパターンを転写します。その後、エッチングなどの手法を用いて回路パターンをウェーハ上に定着させます。
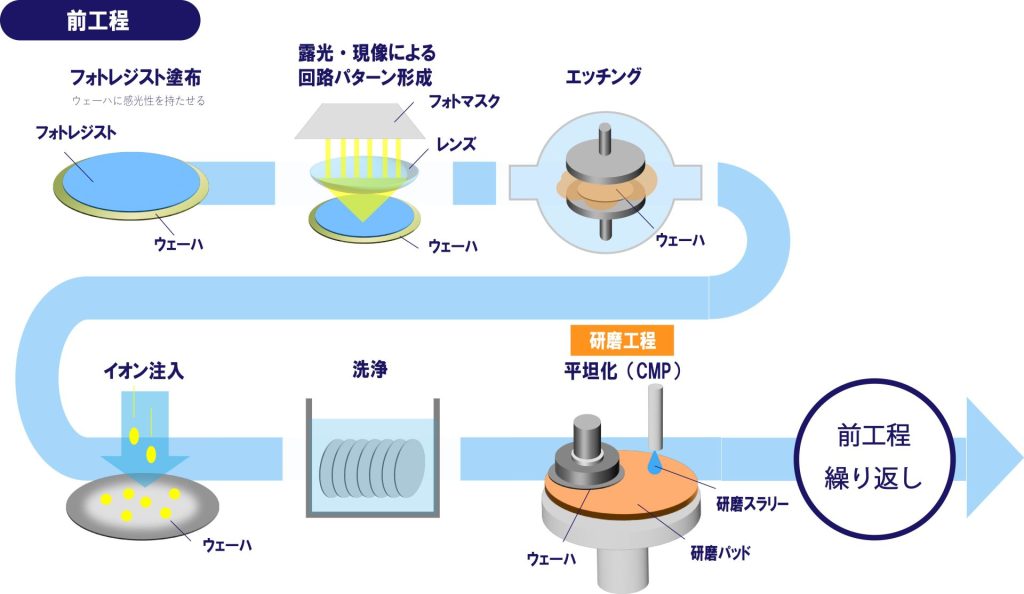
後工程
後工程は、ウェーハを切り分けて、配線や樹脂を封入し組み立てる工程です。はじめにウェーハを四角く切り分けて、ICチップの形を作ります。できあがったチップを、薄い金属で作られたフレームに固定し、金線で接続します。そして、チップを傷や衝撃などから保護するために樹脂モールドによるパッケージングを行います。
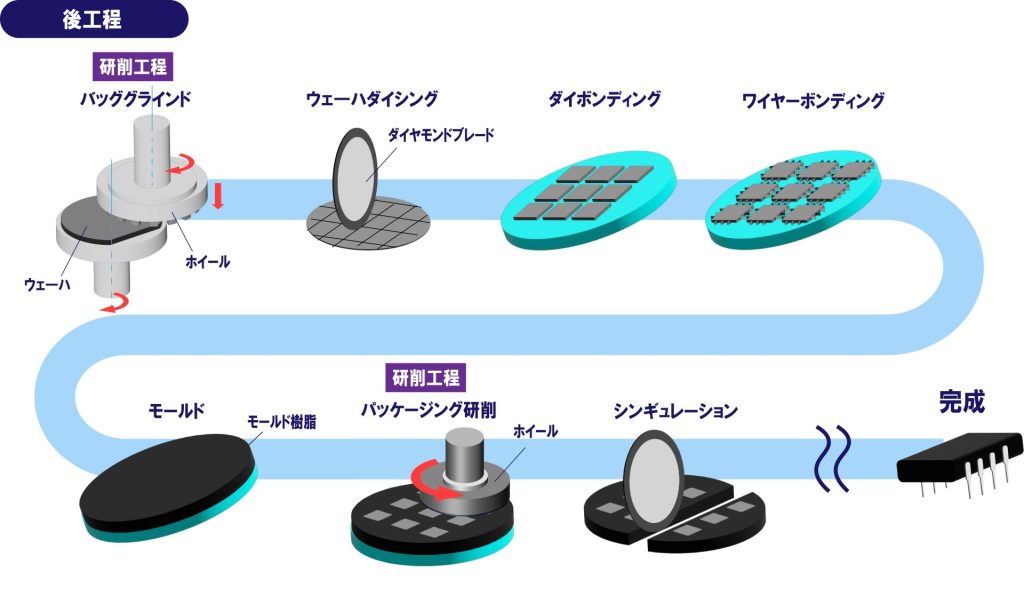
半導体製造における7つの研削・研磨工程とその目的
半導体製造工程において重要な役割となる、7つの研削・研磨工程を以下より説明します
インゴットの外周研削
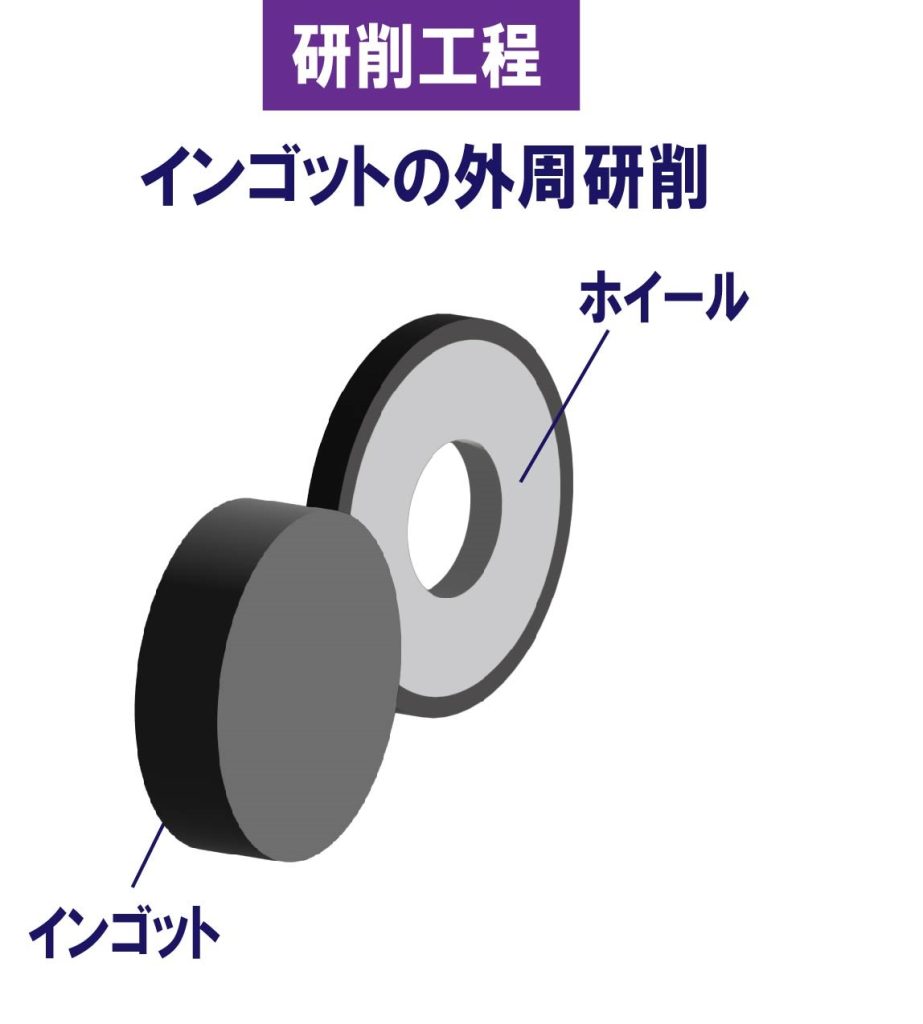
インゴットは半導体ウェーハの基板の原材料となる、結晶成長で得られる円柱状の単結晶の塊です。製造後のインゴットは直径が不均一のため、既定の直径となるよう外周研削を行います。ここでは一般的にレジンホイールが使用されます。
オリフラ・ノッチ加工
オリフラ・ノッチ加工とは、ウェーハの結晶方位を示すために目印をつける加工です。
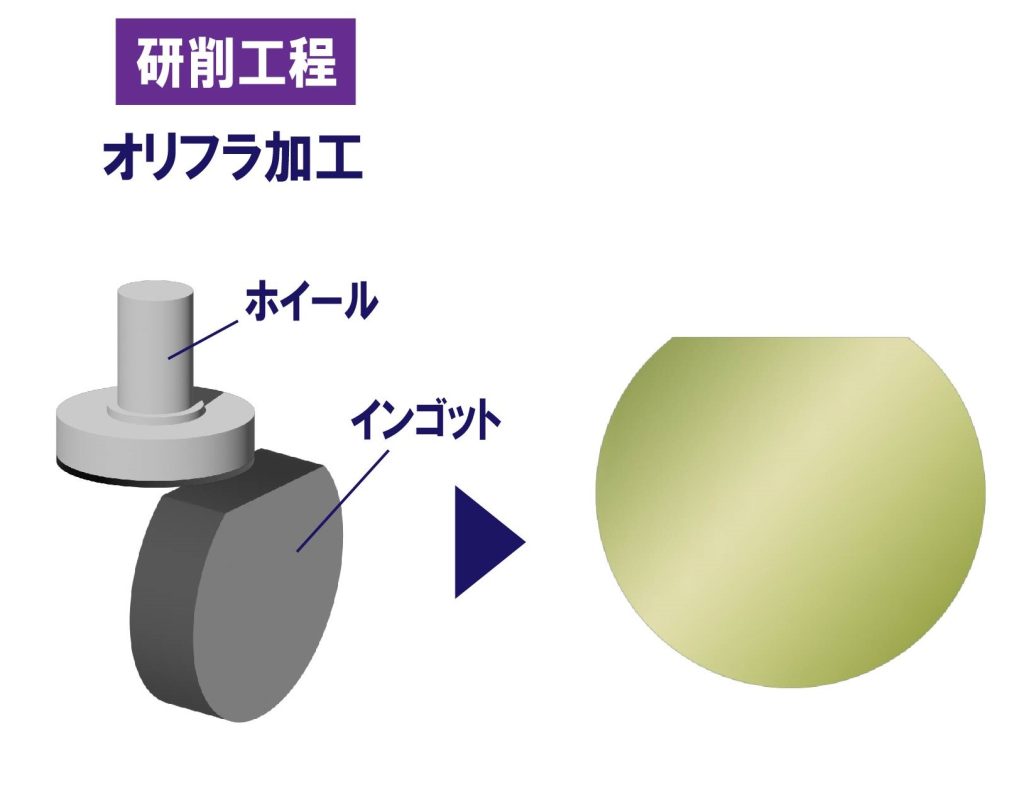
オリフラ加工では、一般的にレジンホイールが使用されます。
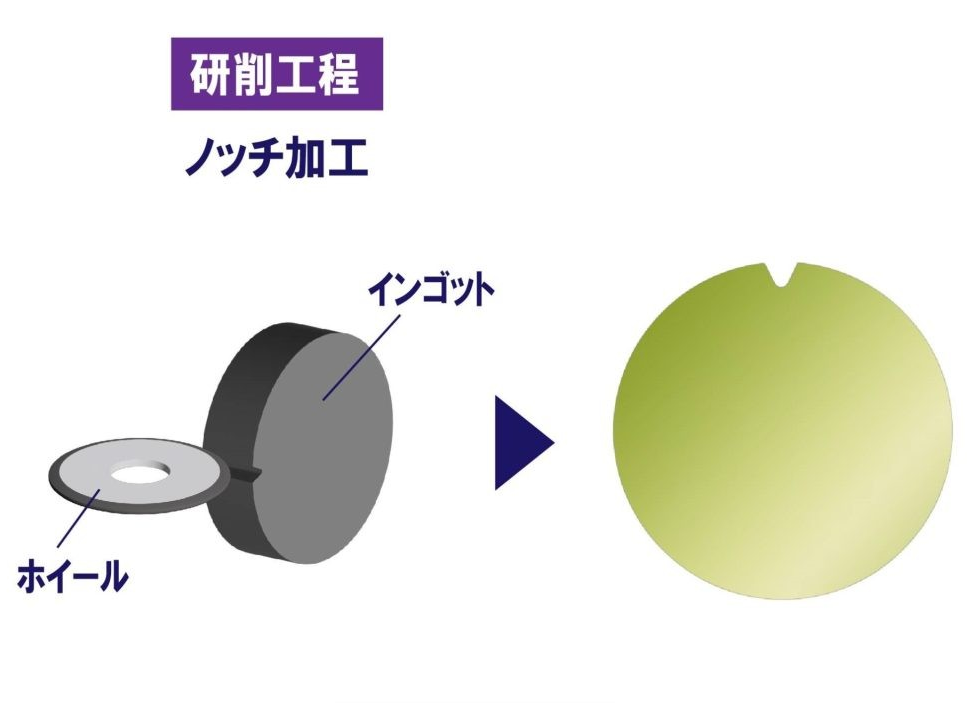
ノッチ加工では、一般的にメタルホイールが使用されます。
べべリング加工
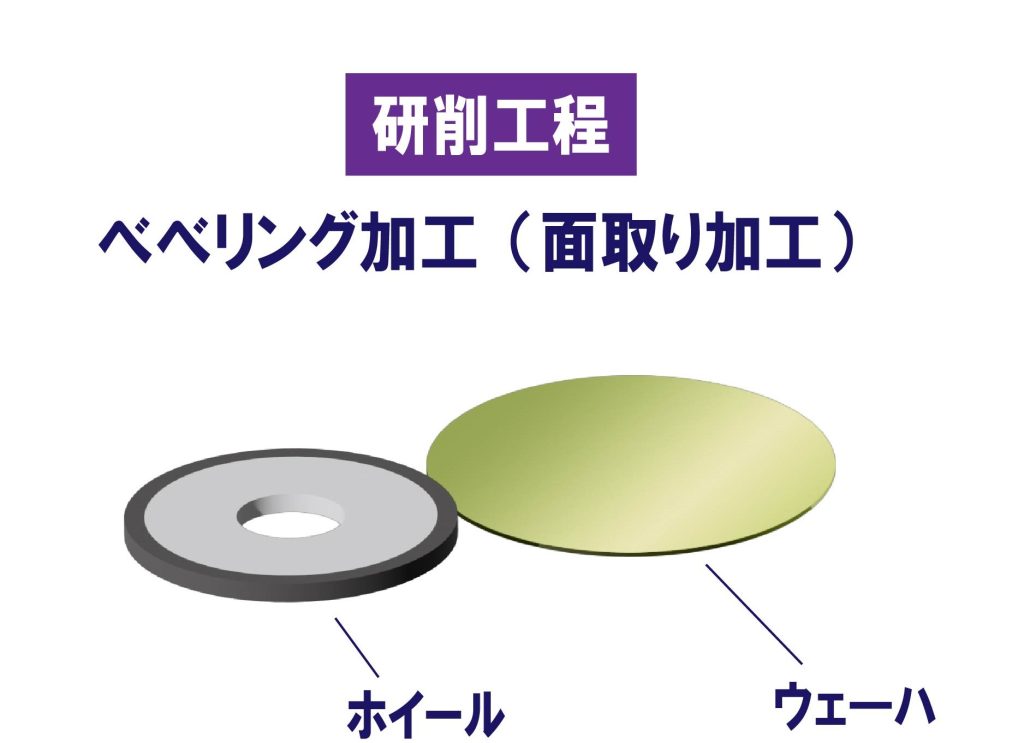
ベベリング加工とは、ウェーハ外周部の面取りを行う工程です。半導体ウェーハは広くは脆性材料であり、CMP工程やハンドリングにおいてウェーハ角部に外力がかかると、チッピングや破損してしまうリスクがあります。ベベリングによる面取りで角部を滑らかにすることで、それらリスクを低減する事ができます。一般的にメタルホイールが使用されます。
ウェーハ表面の研削・研磨
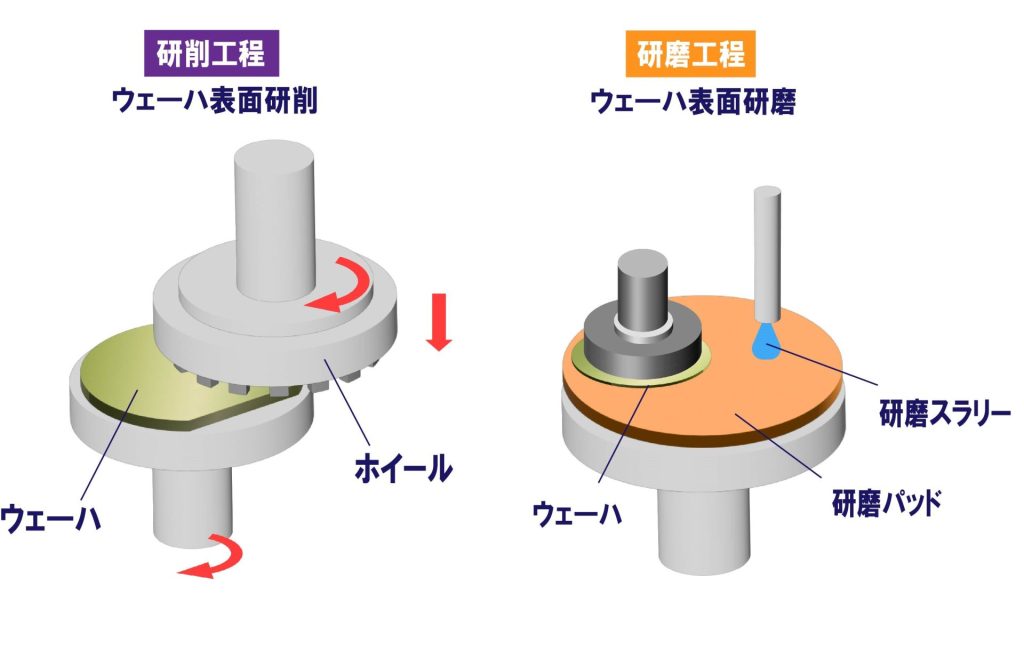
スライシング後のウェーハ表面には凹凸があり、回路を焼き付けるためには、その凹凸を除去する必要があります。ウェーハ表面の研削・研磨工程で表面の平坦化と加工変質層の除去を行います。研削工程では一般的にビトリファイドダイヤモンドホイールが使用されます。
多層配線形成におけるCMP研磨
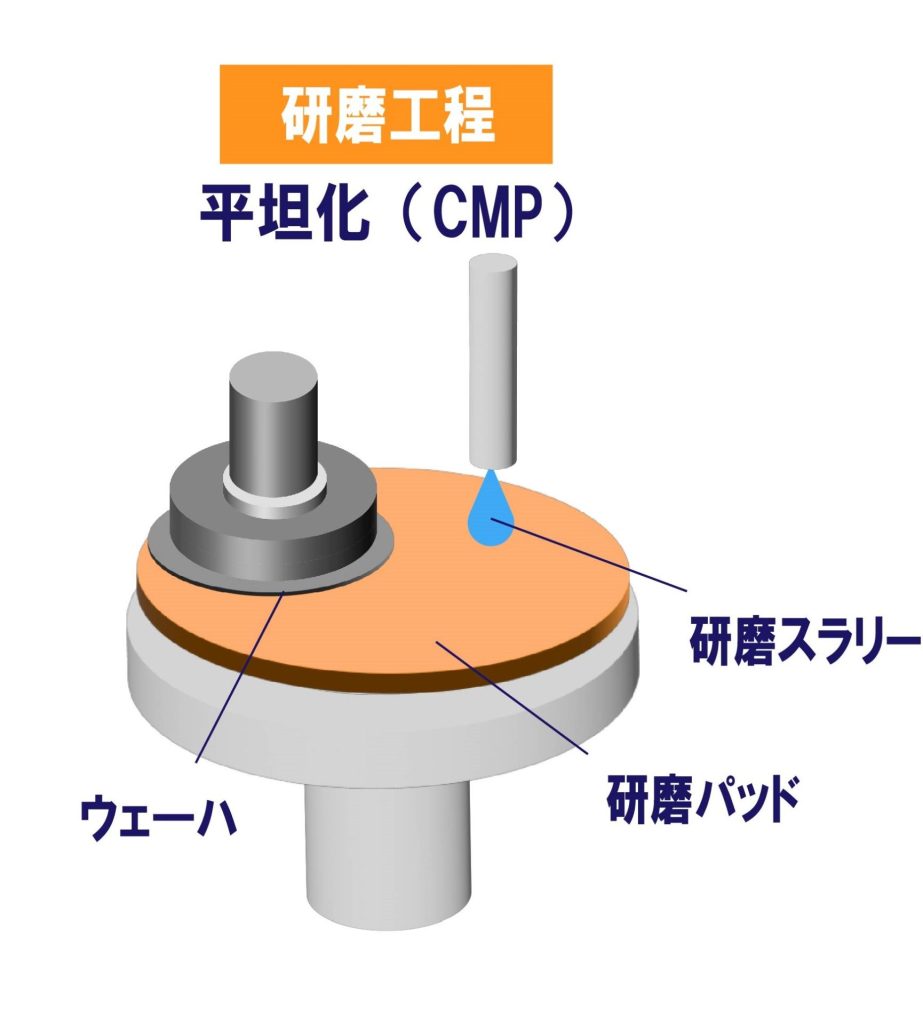
ウェーハ上に複数の金属配線層や絶縁層を積層する多層配線形成工程では、各配線層上の微細な段差や凹凸をCMP研磨により平坦化します。このときにCMP研磨を行う目的は、段差や凹凸が原因で生じる配線の断線や信頼性の劣化、露光工程でレンズの焦点距離が変動し回路パターンの解像が悪くなることが、ウェーハ性能に大きく影響するためです。
CMP研磨では、研磨スラリーを流しながらウェーハを研磨パッドに押し付け、化学反応と機械的な研磨の2つの作用を組み合わせることにより表面を平坦化します。研磨剤には、ダイヤモンドやシリカ、アルミナ、セリアなどがあり、膜の材質によって使い分けられます。
バックグラインド
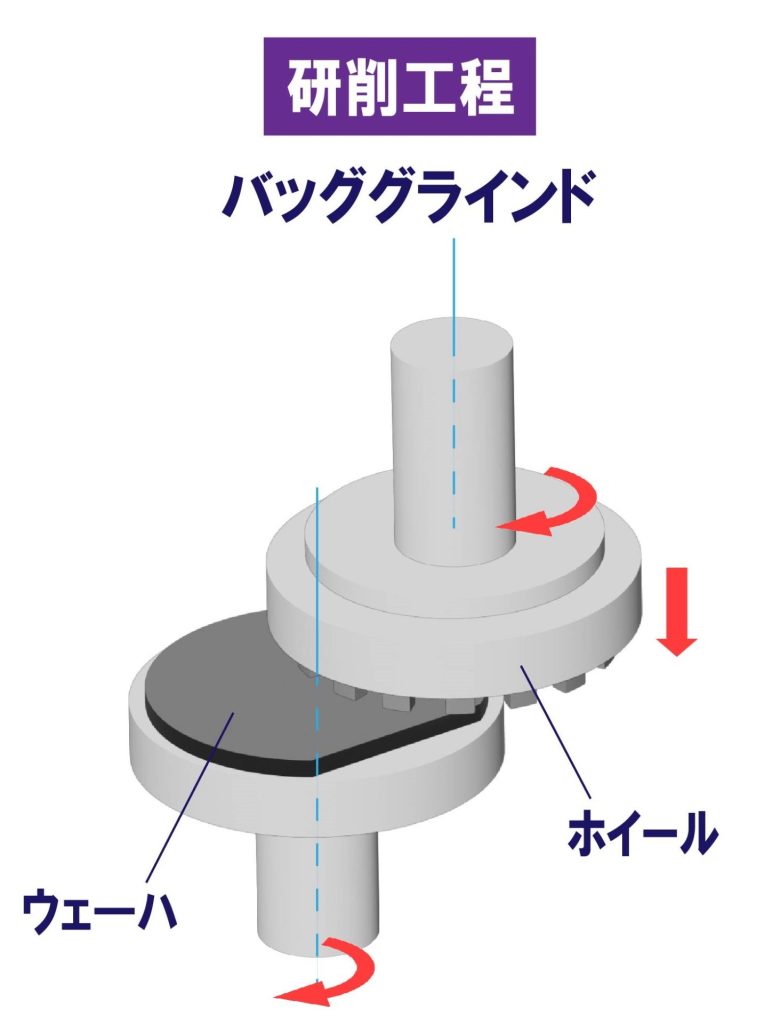
バックグラインドはウェーハに回路を形成したのちに半導体性能に直接影響しない裏面を削ることでウェーハの厚みを薄くする工程です。ウェーハを薄くするほど完成したデバイスの小型化につながります。一方で薄いほどウェーハの反りやハンドリング中の破損が発生しやすくなる等、製造上のリスクも発生します。一般的にビトリファイドダイヤモンドホイールが使用されます。
パッケージング研削
半導体製造における研削・研磨工程の技術
半導体製造における研削・研磨工程は、加工の微細さと高い精度が求められる重要な工程です。以下では、研削・研磨それぞれの技術と使用される工具・材料について詳しく解説します。
半導体製造における研削・研磨工程の技術
半導体製造における研削技術
ダイヤモンド砥粒を使用した工具による研削
ダイヤモンド砥粒が結合剤によって固定された研削ホイールを用いて、ウェーハ表面を研削します。工程としては粗工程と仕上げ工程に分かれています。粗工程の目的は、ウェーハを狙った厚みに削ることです。仕上げ工程の目的は、決められた表面あらさや平坦性を確保することで、粗工程と比べて仕上げ工程では粒径の小さな砥粒が使用されます。
使用される工具
研削ホイール
砥粒としてはダイヤモンドを用います。また、結合剤としてはビトリファイドボンドを用いるのが主流です。半導体製造の研削工程改善には、研削状態から研削盤・ウェーハ材質に合わせてホイール仕様を調整する必要があります。安定した連続加工ができることとホイール摩耗のバランスを加味した上でホイール仕様を選定することが重要です。
ジェイテクトグラインディングツールでは、ホイール選定・加工条件調整などウェーハ研削における技術サポートを行っておりますので、お気軽にお問合わせください。
半導体製造における研磨技術
CMP (Chemical Mechanical Polishing)
CMPとは、化学研磨剤と研磨パッドを使用し、化学反応と機械的な研磨の2つの作用を組み合わせることで、ウェーハ表面の凹凸の平坦化と加工変質層を除去するための加工技術の一種です。高精度な平坦化と鏡面化を実現することが可能です。
使用される工具・材料
研磨パッド
研磨パッドは、柔らかいポリウレタンやポリイミドなどのポリマー材料でできた円盤状のパッドです。このパッドの表面には、微細な孔や溝があり、この構造に研磨砥粒が保持されることで、表面を少しずつ削ることができ、ウェーハ表面が平坦化・鏡面化されます。 研磨パッドには、ウレタンパッド、不織布パッド、スウェードパッドなど様々な種類があります。工作物や目指す仕上がりに合わせて、素材、形状、硬さなどを選定することが重要です。
研磨スラリー
研磨スラリーとは溶液中に研磨剤として砥粒が分散されたものです。これらの研磨剤は、ウェーハ表面の不均一な部分を除去する役割を果たします。工作物や目指す仕上がりに合わせて、研磨剤の粒子サイズを選定することが重要です。
半導体研削用ホイールに求められる品質
微細加工と高精度が求められる半導体研削工程において、研削ホイールの品質は製品の品質や生産効率に直接影響を与えます。よって、求められた要求精度を確保でき耐摩耗性に優れたホイールが必要です。研削ホイールの加工後品質への影響の指標として、表面あらさ、ダメージ層深さ、TTV(平坦度)などが挙げられます。
表面あらさ
工作物への砥粒の切込み深さを決める砥粒の粒度は、加工後の表面あらさに大きく影響を与えます。粒度とは砥粒の大きさを表す指標であり、粒度が大きいほど砥粒サイズは細かくなるため、表面あらさを良くしたい場合には、一般的に粒度の大きなホイールを選定します。
ダメージ層深さ(加工変質層深さ)
研削工程においては、ウェーハ表面にダメージ層(加工変質層)が形成されます。このダメージ層は、研削工程の影響で表面の結晶構造が変化したものであり、製品の性能に悪影響を与える可能性があります。ダメージ層は後工程のCMP研磨で除去しますが、このダメージ層深さを最小限に抑えることがCMP研磨工程の負担低減に繋がります。
TTV(平坦度)
TTV(Total Thickness Variation)は、ウェーハ裏面を吸着させた際の厚みの最大値と最小値の差です。研削工程後のTTVが大きい場合、ウェーハ表面に段差による集積回路上での電気的特性の不均一や配線の不均一性が生じ、性能が低下します。そのため、ウェーハのTTVを小さく加工することができる切れ味の良い研削ホイールを選定することが重要です。
ウェーハ研削用ビトリファイドダイヤモンドホイール「nanoVi®」
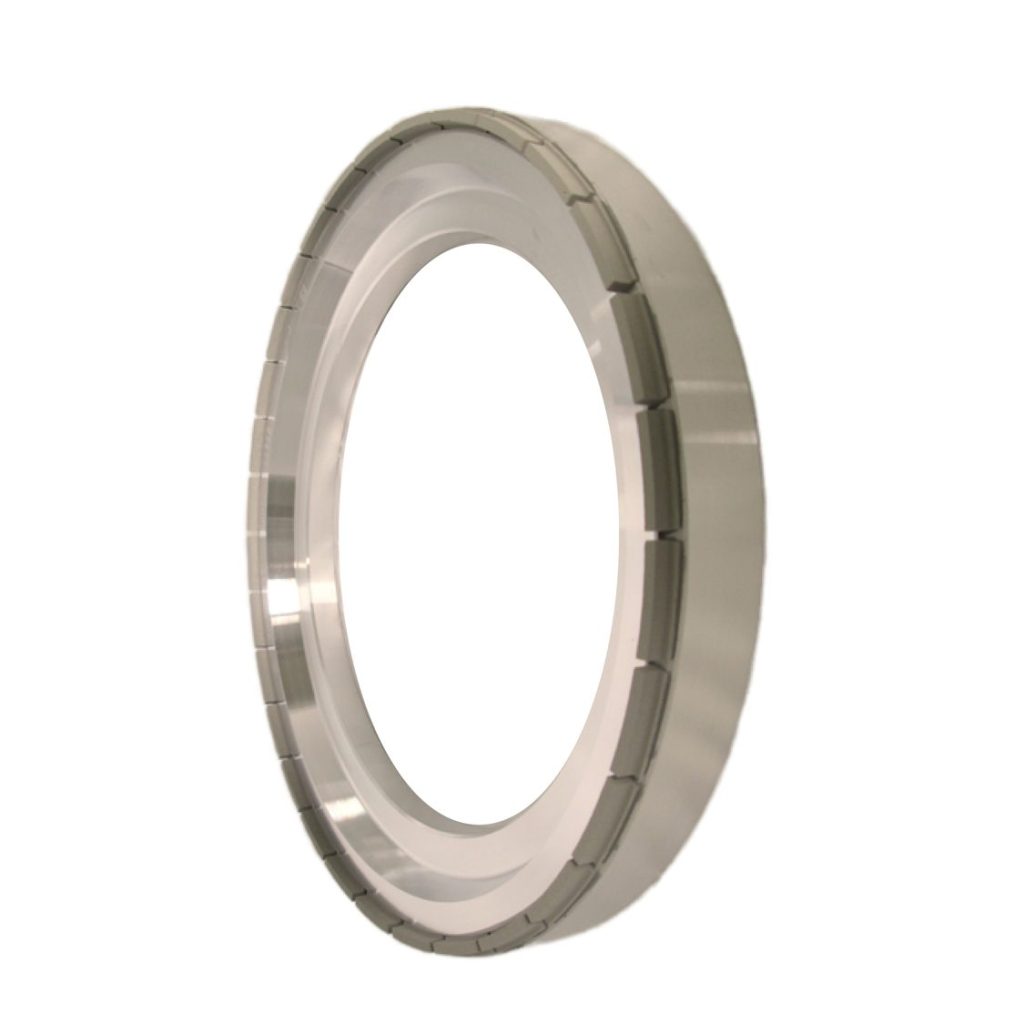
業界最小粒径0.5μmの超微粒ダイヤを均等にする革新製法の開発により、SiCウェーハ研削において優れた切れ味持続性と低摩耗率を両立し、生産性向上に貢献します。
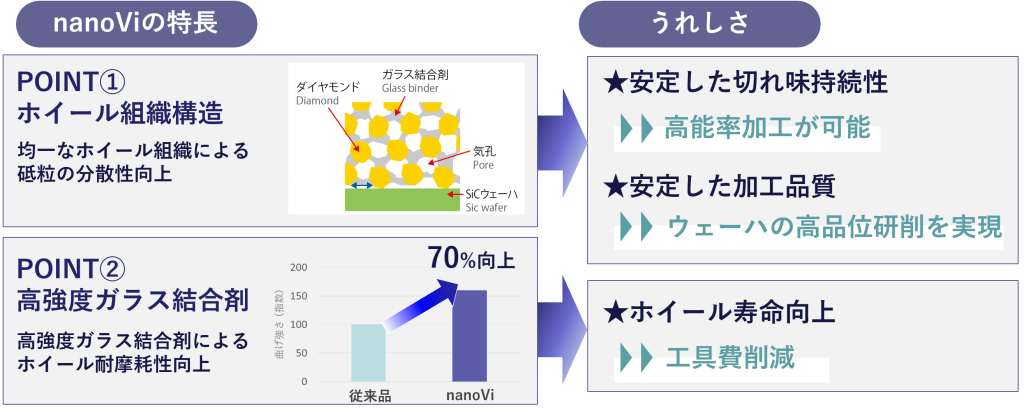
特長
ホイール表面の粗研削工程におけるホイール摩耗量削減
ホイール表面の粗研削において、ホイールの低摩耗率を可能にし、ツールコスト削減に貢献いたします。
ホイール表面の仕上げ研削工程における品質向上
ホイール表面の仕上げ研削において、表面あらさ、ダメージ層深さ(加工変質層深さ)、TTV(平坦度)の低減を可能にし、品質向上に貢献いたします。
8inchのSiCウェーハ研削対応による生産性向上
8inchのSiCウェーハ研削に対応しており、半導体製造の生産性向上に貢献いたします。
製品についてのお問合せや、その他研削加工に関する些細なご相談はこちらからお問い合わせください。