研削焼け(研磨焼け)とは(評価基準・原因・対策について)
研削加工は、高精度な仕上げを求められる部品の製造に欠かせない工程の一つです。しかし、この加工中に発生する「研削焼け(研磨焼け)」は、製品の品質や性能に大きな影響を及ぼします。この記事では、研削焼けのメカニズムから評価基準、そして原因と対策までを詳しく解説していきます。
目次
研削加工で発生する研削焼け(研磨焼け)とは?
研削加工は、研削砥石を高速で回転させ、対象の工作物(加工の対象となる材料)の表面を削り取っていく加工方法です。砥石で工作物を削り取る際の切り屑に生じるせん断と砥石と工作物間の摩擦により、局所的に高温(600~1000℃)が発生します。
この高温が原因で、工作物の表面に変色や変質が生じる現象を「研削焼け」と呼びます。この変色は熱によって工作物の表面が酸化し被膜が形成されることで起こります。焼けの色は、軽度な場合薄いわら色ですが、研削条件が過酷になり温度が上がるにしたがって、褐色、赤褐色、紫、青へと変化していきます。
研削焼けは見た目の変化だけでなく、材料の組織構造や物理的性質にも影響を及ぼし、工作物の表面が硬化したり、微細な亀裂(クラック)が生じたりすることがあります。
研削焼けの組織構造
研削焼けの酸化被膜の組織構造をもう少し詳しく見てみましょう。
研削加工で発生する熱は、工作物の表面を酸化させ、酸化皮膜を形成します。例えば、鉄の場合は酸化鉄が形成されます。
研削加工中の熱が高温になるほど、酸化皮膜の厚みが増し、色調も変化します。つまり、研削焼けの度合いは、皮膜の厚さや色調から評価することが可能です。
酸化皮膜の下層には、数百ナノメートルの酸化物が混ざった皮膜が形成されています。酸化皮膜の表面は比較的緻密で、滑らかな仕上がりとなりますが、その下層は垂直方向に微細なクラックを有しており、これが材料の強度や耐久性に影響を及ぼす場合があります。
研削焼けの影響
研削焼けにより生成される酸化層は、製品や部品の性能や品質に様々な悪影響を及ぼします。
酸化層の存在は、工作物の塗装やめっき工程において結合性を低下させます。さらに、酸化層が工作物の表面を硬化させるため、塗装やめっき以外の後工程での加工が難しくなる場合もあります。
また、酸化層は腐食の促進要因にもなり得ます。酸化層を放置しておくと、その下に残留する微小なクラックが腐食の進行を加速させるリスクもあります。
研削焼けと研削割れ
研削焼けと同様に加工時の熱によって引き起こされる不具合として、研削割れがあります。研削焼けと比較しながら、研削割れの特徴もおさえましょう。
研削割れとは、カーボン含有量の高い鋼が研削加工中に生じる熱により、組織が変化して表面にクラックが生じる現象です。組織中に析出物が形成されたり、体心立方格子の組織が面心立方格子の組織に変化したりすることで体積が変わり、応力がたまって割れが発生します。
一方、研削焼けは、研磨中に発生する熱により素材が焼けて色が変化する現象で、これはカーボン含有量に関係なく発生します。
研削焼けの評価
次に研削焼けの評価方法と評価基準を解説します。目視の他に次のような評価方法が取られることが多いです。
評価方法
評価方法は次の手法が取られることが多いです。
ナイタールエッチング
研削焼け評価に広く用いられるエッチング方法です。試料を酸層に浸すことで鋼や鉄の組織変化を明確に観察することができるため、光学顕微鏡観察と組み合わせて使用されます。これにより、より詳細な素材の変化を評価し、研削焼けの程度を確認できます。
評価基準
研削焼けの評価基準は、製品の用途や性能要件に応じて異なります。一般的には、色変化の程度や範囲、酸化層の厚さ、表面硬度の変化量、腐食試験の結果が評価基準として活用されています。
研削焼けのメカニズム
適切な評価方法と評価基準が求められる研削焼けですが、その発生するメカニズムは、研削加工中の熱発生とその熱の除去不足に起因しています。研削焼けが発生するメカニズムを順を追って説明します。
①熱の発生
研削砥石と工作物の間の摩擦によって熱が発生します。この摩擦熱が、研削の主要な熱源です。
他にも、工作物の材料が研削砥石によって切削される過程で、材料は塑性変形を受けます。この塑性変形の過程で、内部エネルギーが熱エネルギーとして放出されることがあります
(図1)。
図1:切断と研削の加工熱の特性
出典:東京農工大学大学院 工学府 機械システム工学専攻 伊藤幸男「CFRPの研削加工における薄肉砥石を用いた冷風供給の効果と赤外線放射温度計による加工状態モニタリング」(2022)P.7
https://ci.nii.ac.jp/naid/500001542791
②酸化反応
高温になると、工作物の表面の鉄が酸素と反応しやすくなり、酸化鉄の層が形成されます。この酸化層が研削焼けです。
③組織変化
工作物が局所的に高温になると、材料の組織が変化する可能性があります。例えば、鋼の場合、高温によってオーステナイト組織が形成され、急速に冷却されることでマルテンサイト組織が生じることがあります。
研削焼けの原因(熱の発生原因)
研削焼けの原因となる加工熱は様々な要因から発生します。熱を完全に無くすことは不可能なので、原因を網羅的に把握した上で優先順位を持って対策をしていくことが必要です。まずは考えられる原因を見ていきましょう。
研削条件
まず原因として挙げられるのが、砥石の周速度や送り速度、切込み量です。高速な研削は熱の発生を増加させ、送り速度の増加は摩擦とともに発熱を引き起こします。また、深い切り込みは大きな熱を発生させる可能性があります。さらに、多数の研削パスによって熱が累積する可能性も考慮する必要があります。
砥石の仕様や状態
摩耗したり詰まったりした砥石は発生する熱が増加します。そして、砥石の摩耗や目詰まりが摩擦を増加させ、それがさらなる熱の発生につながるという悪循環を生み出します。
ツルーイング条件
ツルーイング(形直し)の頻度は砥石の性能に影響します。頻繁に行わないと、摩耗や目詰まりが生じて摩擦が増えます。しかし、過度に行うと砥石が消耗し性能が低下してしまいます。
ツルーイングの深さや圧力、速度も重要です。 ツルーイングが深すぎると、新しい砥粒が露出し研削初期に多く熱が発生する場合があります。また、ツルーイングの圧力や速度が不適切だと摩擦や熱の発生が増加します。
ツルアの仕様や状態
ツルアはツルーイングを行うための部材です。ツルアの材料や形状が砥石の種類や用途に合っていない場合、熱が発生しやすくなります。
ツルアが過度に摩耗していたり、ツルアに使用されているダイヤが過度に脱落していたりすると、砥石の表面を均一に整えることができません。
工作物の寸法や取り代
工作物の特性は、研削焼けの発生に深く関わっています。材料の熱伝導性や硬さが影響を与え、それらが熱の発生や分散のパターンを左右します。
研削液(研削盤)
クーラントノズルの位置や向き、流量が不適切だと熱の除去が不十分となり、研削焼けの原因となります。特にノズルの詰まりが起きた場合、研削液の供給不足から研削中の熱の除去が十分に行えず、研削焼けにつながります。
種類や濃度については、研削液は大きく水溶性と油性に分けられます。水溶性の研削液は冷却効果に優れ、油性の研削液は潤滑性が高いため、使用する工作機械や加工する材料によって適したものを選定しなければなりません。
また、研削液の濃度が不適切だと、冷却効果や潤滑性が損なわれます。例えば、濃度が高すぎると粘度が上昇し、冷却効果が低下します。
研削焼けの対策
研削焼けの主な原因が特定できたら対策を実施していく必要があります。まずはコストがかからない対策を優先的に進めることをおすすめします。
研削条件の対策
研削焼けのリスクを最小限に抑えるための研削条件の対策としては、以下の3つが挙げられます。
砥石周速度
研削焼けを避けるためには、中速または低速範囲での研削が推奨されます。高速での研削は熱発生を促進するため、特に熱に敏感な材料の加工時には低速研削を選択しましょう。
送り速度
送り速度を低く設定することで、摩擦熱が抑制され、それに伴い熱発生も抑えられます。
切込み量
一度に削除する材料の量を抑制するために、浅い切り込みを選択することも研削焼けの防止に寄与します。大量の材料を一度に削ると、大量の熱が発生してしまいます。浅い切り込みを選択することで、研削焼けのリスクを低減させることができます。
ただし、切り込み量が浅すぎると砥石の砥粒が滑り、研削熱が増える場合があるので注意が必要です。
砥石の仕様や選定
熱伝導性の低い結合剤や摩擦係数の低い砥粒の砥石を選択することが一つの解決策です。また、粗い粒度の砥石を用いることで摩擦熱を低減することも可能です。
ツルーイングによる砥石の目直し
ツルーイングを行うドレッサの材質、形状、サイズを適切に選択することも重要です。さらに、ツルーイングの頻度にも注意しましょう。ツルーイングは研削石の表面が摩耗したり、詰まったりする前に、定期的に行うことが推奨されます。
研削液
熱の発生を効果的に抑制するためには、冷却性能を持つ研削液の選択が推奨されます。供給する研削液の量も重要で、研削エリアに十分な量を供給することで熱の発生を抑えることが可能です。さらに、クーラントノズルは研削エリアに直接当たるように向けましょう。
ジェイテクトグラインディングツールの超砥粒ホイール
ジェイテクトグラインディングツールはトヨタグループ唯一のダイヤモンド工具メーカーで、多岐にわたる製品の研削用ダイヤモンド砥石やドレッサを製造しています。その開発力と技術力で、世界一のものづくりを目指しています。
研削(研磨)焼け・研削割れを抑制するビトリファイドCBNホイール「削楽~SAKURA~」
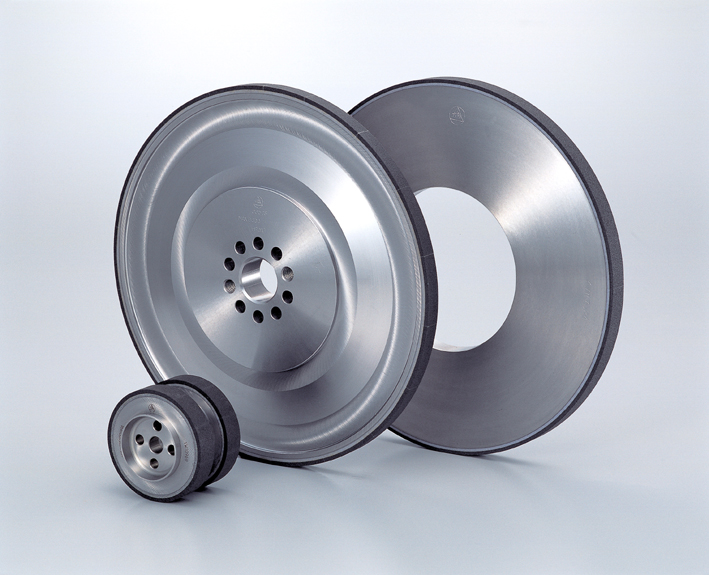
”削楽~SAKURA~”は、新開発多気孔構造による擦り抑制により、余分な発熱を抑制し研削(研磨)焼け・研削割れを改善します。
また、CBN砥石層を構成する主要要素であるCBN砥粒、結合剤、添加剤の構成を一新しました。多くのお客様に長寿命なホイール性能に加え、形状精度の安定や、研削時間が安定といった使い易さを提供致します。
加工事例①研削焼けなくサイクルタイム短縮
研削焼け無くサイクルタイム短縮が可能となり、生産性向上に貢献致します。
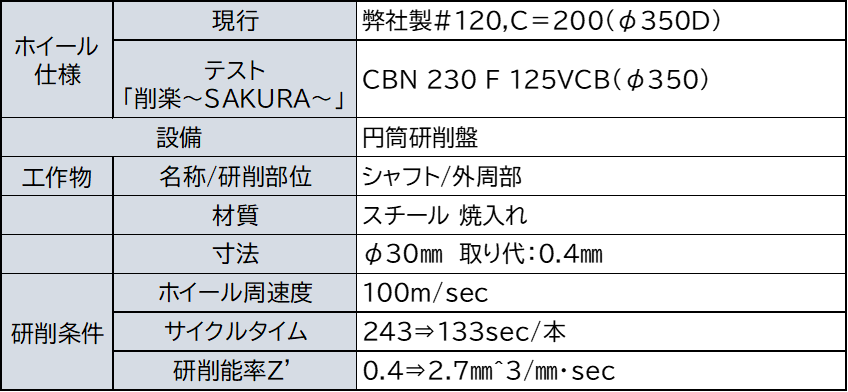
加工事例②研削焼け抑制してインターバル延長が可能
研削焼けを抑制してツルーイングインターバル延長が可能となり、工具費低減に貢献致します。
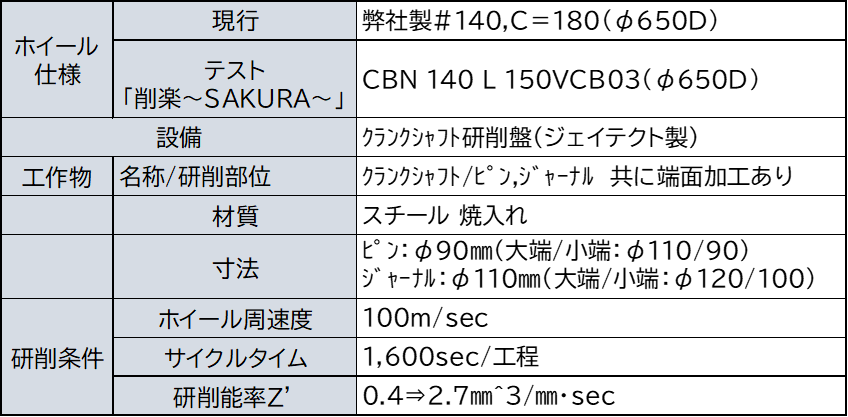
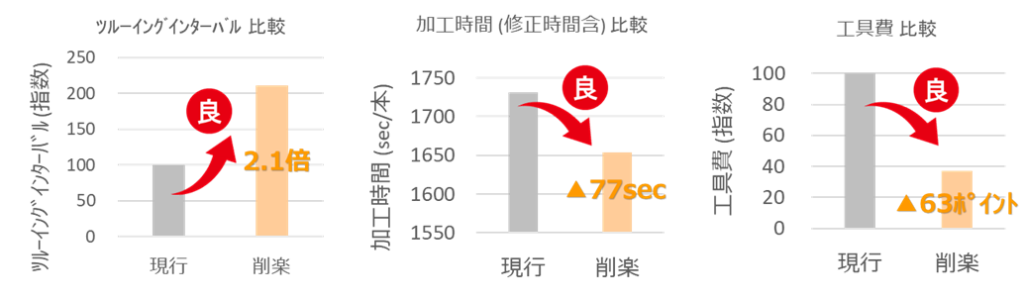
製品についてのお問合せや、その他研削加工に関する些細なご相談はこちらからお問い合わせください。