半導体製造前工程を支える部品加工の重要性
半導体は、ノートパソコンやスマートフォン、自動車、近年話題になっている生成AIなどさまざまな分野、製品に使われています。近年では、IoTの進展により、さらに半導体の需要が高まっています。半導体の需要が強まるとともに、より高品位な半導体製造のために装置・部品の精度や耐久性も重要となっています。今回は半導体製造装置の中でも、特に過酷な環境でのプロセスが多い前工程で使用される装置と、その部品の加工技術について解説します。
目次
半導体製造前工程とは?
半導体製造は、主に前工程と後工程に分けられます。中でも前工程は、ウェーハ上に回路を形成する工程を指し、半導体製造全体の品質を左右する重要なプロセスです。この工程では、露光工程、エッチング工程、イオン注入工程など、過酷な環境での工程が繰り返し行われます。
半導体製造前工程装置の構造部品として選定される材質
半導体製造装置内で使用される部品は、過酷なプロセス環境で繰り返し使用されるため、優れた耐熱性、耐摩耗性、化学的安定性などを持った材料を選定する必要があります。材質選びでは、製造プロセス中にコンタミネーション(不純物の混入)を引き起こさないことも重要です。
材質
上記の条件を満たす材質には、セラミックス、石英、タングステンなどがあります。それぞれの材質の特性と使用されている構造部品について見ていきましょう。
セラミックス
セラミックスは高い耐熱性や耐薬品性、耐プラズマ性を持ち、絶縁体としての性質も優れています。これらの特徴により、高温環境や腐食性のある化学物質が使われる環境でも安定した性能を維持することができるため、CVD装置などの成膜装置やエッチング装置、レジスト剥離装置内のステージなどに使用されることが多いです。
石英
石英は、高純度であることから高い透過性を持ち、熱膨張率が低いため高温環境下での形状安定性が良く、化学的にも安定している材料です。これらの特性から、石英は光学的透明性が求められる露光装置のレンズや、成膜工程における酸化炉、CVD炉内でウェーハを運搬するウェーハボートなどの用途で使用されています。
タングステン
タングステンは金属の中で最も高い融点(3422℃)を持ち、熱膨張率が低いため高温環境下でも形状を維持しやすく、また硬度が高いため耐摩耗性に優れるという特徴から、高温炉内の部材として選定されることが多いです。他にも成膜工程におけるスパッタ装置内のターゲット材などで使用されています。
半導体製造前工程のどこで使用されているの?
上記のような材質が実際に半導体製造前工程のどこで使用されているのか、製造工程の流れから解説していきます。
成膜工程
半導体デバイスは、導体膜や配線、絶縁層など複数の層で構成されています。この工程では、ウェーハ表面を精密洗浄した後、成膜装置でウェーハ表面上に薄膜をコーティングします。成膜装置には、熱酸化装置、CVD装置、ALD装置、スパッタ装置、めっき装置などがあります。
ウェーハボート
酸化炉、CVD炉内では石英を使用したウェーハボートにより、ウェーハを運搬します。
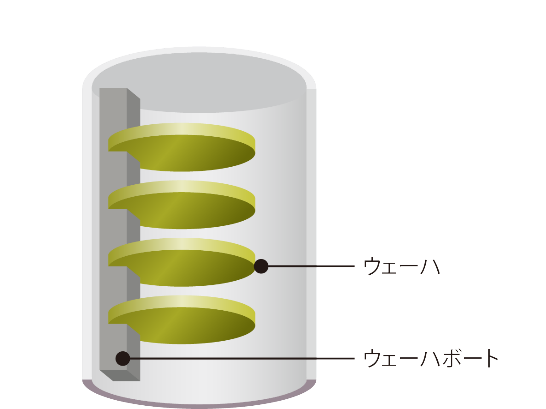
ターゲット材
スパッタ装置内ではターゲット材が使用されています。
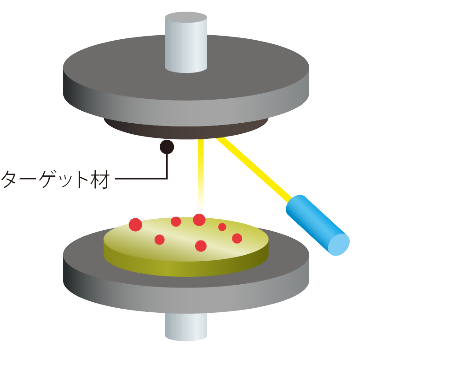
露光工程
ウェーハに塗布したフォトレジストに、光(紫外線)でフォトマスクのパターンを転写します。露光装置のステージには、環境温度の変化に対する耐久性やその寸法変化などを考慮する必要があるため、低熱膨張ガラスが使用されています。
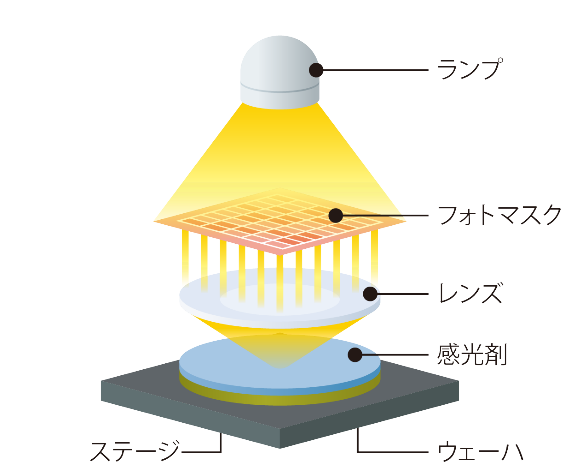
エッチング工程
エッチング装置では、現像機で溶かしたフォトレジストの下の、不要な薄膜の一部を除去して、必要なパターンのみを残します。
イオン注入工程
イオン注入装置では、イオン化した導電型不純物を、高電圧で加速させることでウェーハ表面に注入します。これにより、ウェーハ表面にP型とN型の領域を形成し、半導体に電気の流れを作り出します。
レジスト剥離工程
回路パターンの作成に必要な工程が完了したら、フォトレジストを剥離します。
静電チャック
エッチング装置やイオン注入装置、レジスト剥離装置内では、静電チャックによってウェーハを固定します。静電チャックとは、電気的な力でウェーハを吸着させる機器です。材質には、アルミナ、SiC、MMC(金属セラミックス複合材料)などが選定され、吸着性が均一であることやウェーハのダメージや吸着痕がないことが特徴です。
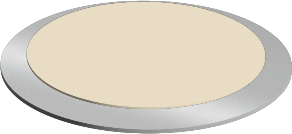
その他の半導体製造工程では、検査工程や搬送などでセラミックス治具が使用されています。
検査用
半導体製造工程では、ウェーハ製造時、回路形成時、パッケージング時などで、各種検査装置を使用して検査が行われます。検査用装置内のウェーハ固定にも、静電チャックが使用されています。静電吸着が困難な場合は、真空チャックが使用されます。
静電チャック、真空チャック
検査用でウェーハの固定に使用するチャックには「静電チャック」と「真空チャック」があります。電気的な力でウェーハを吸着させる「静電チャック」の他に、吸引力でウェーハを吸着させる「真空チャック」を使用する場合もあります。真空チャックは、工作物が濡れている場合や厚みがあり沿っている場合など、静電吸着が困難な場合に有効的です。
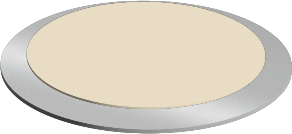
ウェーハ搬送用
工程間のウェーハの移し替えには、搬送用ロボットが使用されます。特にロボットのハンドはウェーハに直接接触するため、耐摩耗性や耐熱性、コンタミなどの観点からSiCやアルミナが選定されることが多いです。
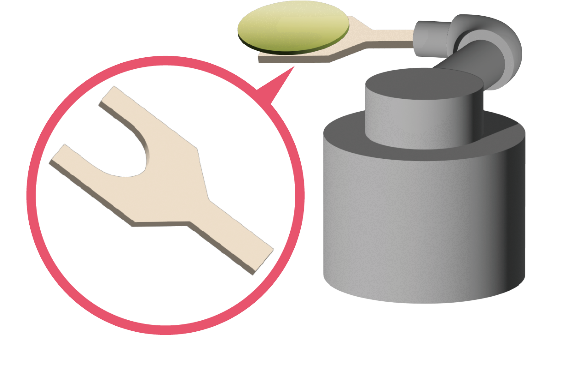
半導体製造装置の部品加工技術
半導体は微細な傷さえ許されない繊細な製品であり、特にウェーハに直接接触する部品には高い寸法精度と滑らかな表面が要求されます。それらの部品として使われる特にセラミックスのアルミナやSiCなどは、硬脆性材料であり加工が難しいという課題もあります。本章では、半導体製造装置部品の研削加工技術について解説します。
半導体製造装置部品の研削加工
研削加工は研磨しながらワークを削っていく加工方法で、表面を滑らかに仕上げたい場合や、高い寸法精度の加工が必要な場合に用いられます。半導体製造装置部品として選定されるセラミックス、タングステンなどは耐摩耗性の特徴もあり、非常に硬い材料であるため、研削加工による表面仕上げが重要です。
半導体製造装置部品の研削加工事例
上述のとおり、半導体製造の前工程の構造部品として選定される材料には、過酷な環境に対する耐久性が高い反面、加工が難しいという課題もあります。本章では、当社でのSiC、アルミナなどのセラミックス、炭化タングステンを材料としたターゲット材、石英を材料としたウェーハボートなどの半導体製造装置部品における加工実績をご紹介していきます。
▼半導体製造装置部品の研削事例集公開中▼
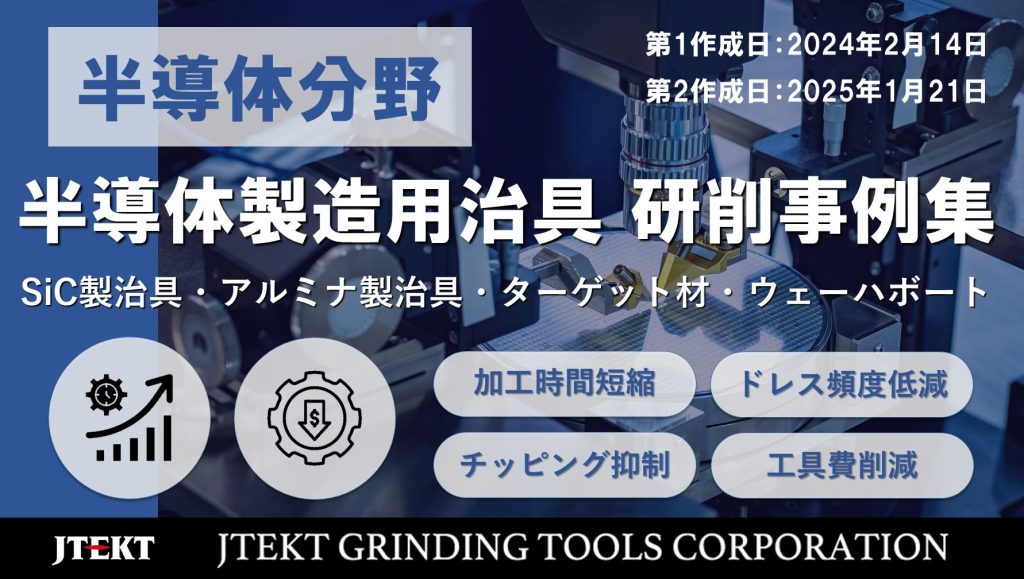
SiC製治具の研削加工事例:加工時間 67%短縮
ジェイテクトグラインディングツールのレジンホイール「レボメイト」を用いてSiC製治具の平面研削を行ったところ、切込み量が他社製レジンホイールに比べ65%向上。これにより、加工時間が67%短縮され、生産性が向上しました。
アルミナ製治具の研削加工事例:加工時間 20%短縮
ジェイテクトグラインディングツールのレジンホイール「レボメイト」を用いてアルミナ製治具の平面研削を行ったところ、切込み量が他社製レジンホイールに比べ20%向上。これにより、加工時間が20%短縮され、生産性が向上しました。
石英ウェーハボートの研削加工事例:チッピング抑制
ジェイテクトグラインディングツールのメタルホイール「テラメイトMT3」を用いたウェーハボートの溝切り加工を行ったところ、他社製ホイールに比べて研削抵抗を低減しチッピング量の抑制を実現しました。
ターゲット材(炭化タングステン)研削加工事例
ジェイテクトグラインディングツールのレジンホイールを使用して平面研削を行ったところ、他社製ホイールに比べて切り込み量が6倍、ドレスインターバルが4倍、ホイール寿命が2.5倍向上しました。これにより、加工時間短縮、ドレス頻度の低減、工具寿命の削減を実現しました。
コンタミや破損が許されない半導体製造工程では、研削加工によって部品の表面品位を確保し、半導体ウェーハの搬送や保持に最適な部品に仕上げることが重要です。半導体製造装置部品の研削加工でお悩みなら、ぜひジェイテクトグラインディングツールへご相談ください。